A Technical Sales Approach
Visual inspections and tests to perform when visiting customers
By Nathan Olszak
In this changing market, one thing is certain: We are all in need of better, faster information. More customers today are requesting solutions to their water treatment equipment problems and they are expecting this information in a timely manner.
I have noticed that there is a similarity between sales calls and audits performed on existing equipment, and tests and audits performed on equipment pretty much remain the same on every call. For each call, I am armed with a test kit, pen and paper-and that is all I need.
The following is a list of visual inspections and tests to perform on equipment and why these should be performed. Use this as a guide when visiting with your customers.
Softener System Inspections
Check exterior piping and tanks for leaks. By making sure there are not any leaks present that could become big gushes of water, you can save a lot of time and help your customer take care of a small issue before it becomes a large one.
Check the water level in the brine tank. A high water level can mean that the brine valve is leaking. If the brine valve is not fixed, it will eventually fail and continue to overfill the tank causing the salt to dissolve and waste to drain.
Check pressure gauges. Checking the pressure gauges on the inlet and outlet can determine various things. Many controllers and systems today need minimal pressure to operate properly. A high pressure loss could result in clogged distributors, valves not opening, valves not closing and resin breaking down.
Check the control. Many electronic controllers today offer the ability to view a lot of valuable information, for example: average usage for seven days a week; peak flows and at what times they occur; how many gallons remain; and at what capacity a system is set (i.e., how many gallons or grains of capacity). Knowing this information can help determine if the system is working beyond its designed capacity or if the system resin is breaking down.
Check the control valves. Checking the control valves can determine if there are signs of wear and tear. Checking the weep holes on an Aquamatic valve or the piston assembly on a Fleck valve can help avoid future problems. If the weep hole is leaking, you then know it is time to start thinking about rebuilding the valve.
Check the drain. Check the drain to see not only if it is leaking but also if there are signs of resin in or around the drain. If resin is present, it may be showing signs of degradation, and further inspection inside of the tank may be necessary. The other reason to inspect the drain-to see if it is leaking-is because if a softener is not in regeneration, there should not be water flowing to the drain. If it is, this is a sign that the valves are failing and you will need to repair or rebuild them.
On a nest of a valve or multiport valve system, testing the drain water for hardness can help you determine which valve has failed-if it is hard, then it is the backwash valve; if it is soft, then it is the flush valve.
Water Testing
Test for hardness. Testing both the inlet and outlet for hardness can help determine several things. Testing the inlet can first determine the hardness level. Armed with this information, you can determine if the electronic controller is set properly. If the controller is set lower (meaning the gallons/capacity is at a lower output than what the system is capable of doing) it may mean that the resin is losing capacity and needs to be tested or replaced.
If you find that the resin is breaking down, based on current capacity and demand you can figure out what the system is wasting in water usage and salt. By testing the outlet of the softener, you can determine if it is producing soft water.
On larger systems, testing at the bottom of the tank-if accessible-can determine if there is a valve problem.
Test for conductivity. Testing conductivity from the inlet and outlet will help determine whether or not the softener has gone through a complete regeneration and if the salt has been rinsed out from the softener before it has come online.
Test for iron. One good reason to test for iron is because of changes in the influent water. Iron is not good for resin and can hinder its performance, especially if it is oxidized iron. Clear-water iron can be removed by some resins up to a certain amount. Check with your resin distributor before determining what resin is good for your system.
A Better Understanding
After performing these tests, you will have a better understanding of how the equipment is performing and what is in need of repair. Knowing what is wrong, or what could potentially go wrong, will give you the upper hand when explaining to your customer what needs to be done and the reasons why.
Once your inspection is complete, talk to your customer and explain exactly what you found and whether or not they will need to take action.
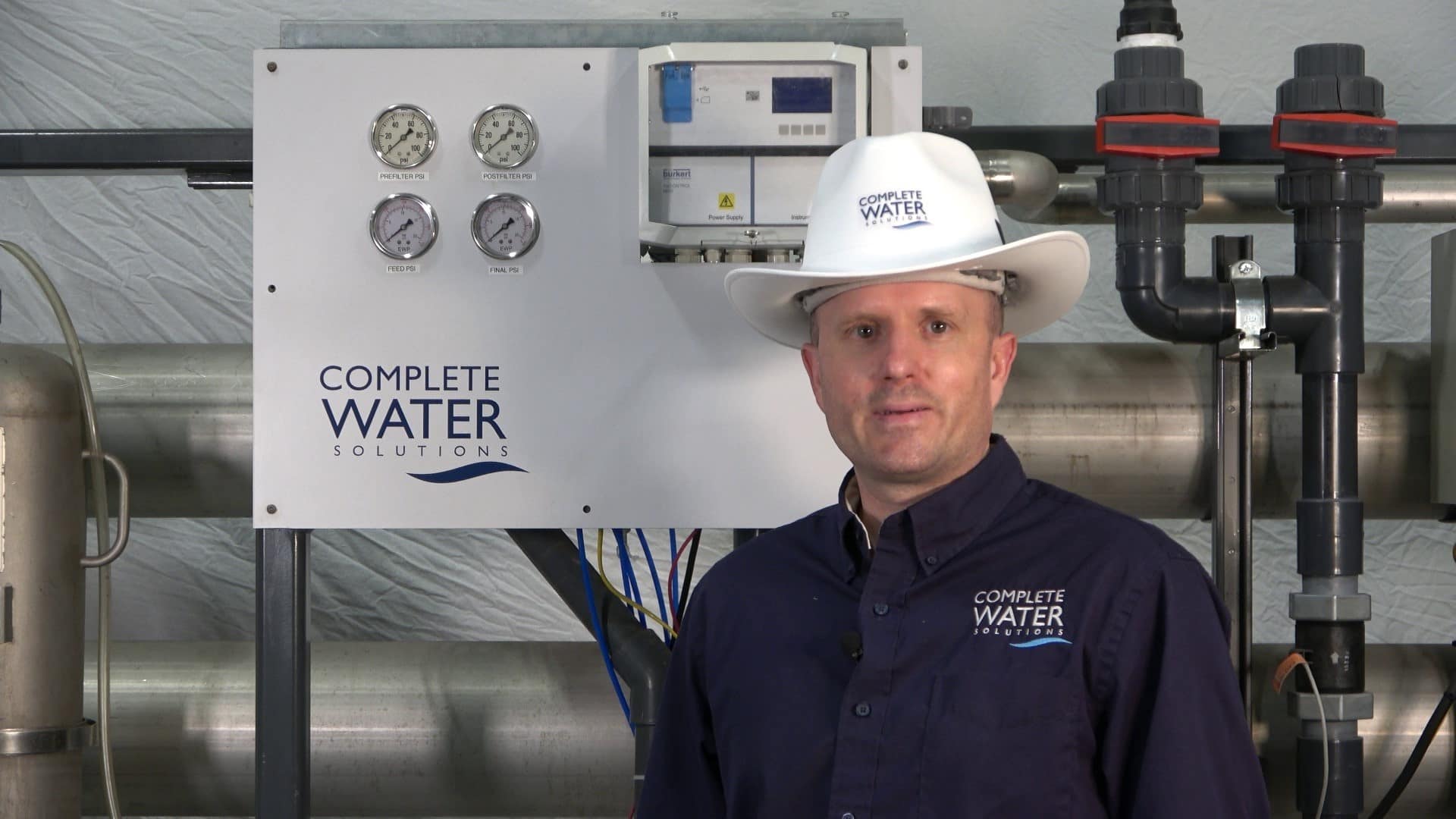
With over 30 years of hands-on experience in the water treatment industry, Nathan Olszak is a trusted water treatment expert. He specializes in designing, engineering, and servicing water treatment systems. As the owner of Complete Water Solutions, Osmonics, and Membrane Cleaning Pro, Nathan has built a reputation for delivering customized water treatment solutions that enhance efficiency, reliability, and water quality across various industries, including the medical, commercial, and manufacturing sectors.
Nathan’s journey in water treatment began as a service technician. He gained in-depth knowledge by working with all major brands of equipment, including Veolia, Suez, Bruner, Culligan, Pentair, Aquamatic, Osmonics, GE Water, Marlo, Lakeside, Fleck, Autotrol, US Filter, ION Pure, Siemens, Evoqua, and many others. This hands-on expertise, combined with his technical certifications, has made him a leader in water system engineering and water management.
Credentials & Expertise
- Certifications: David H. Paul Reverse Osmosis Certification, PLC Programming
- License: Power Plant Operating Engineer 3rd Class
- Specialties:
- Design & engineering of water treatment systems and advanced water systems
- Custom water filtration systems and solutions
- Installation, automation, and repair of water treatment systems
- Expertise in Reverse Osmosis (RO), Deionization, Water Softening, Carbon Filtration, Iron Filtration, UV Treatment, Ultrafiltration (UF), Process Filtration, CEDI/EDI, and more
- Specialized knowledge in Boiler Feed Water, Tower Makeup Water, and drinking water production for industries such as bottling, pharmaceuticals, and food processing
- Project management and reclaiming of water system waste for other uses
- Evaluation of raw water sources and potential contamination risks
- Industrial water treatment strategies to prevent corrosion and optimize system performance
- Boiler water treatment to enhance energy efficiency and system longevity
Nathan’s commitment to excellence extends beyond equipment sales and service. He works closely with clients to develop tailored water treatment services that optimize performance and meet their operations’ unique demands. His expertise covers methods that mitigate water impurities, ensure fresh water accessibility, and maintain regulatory compliance. It also includes the design of high-efficiency reverse osmosis systems for industrial use.
Nathan focuses on the latest technology in water conditioning, water softeners, filters, and pumps to improve maintenance and efficiency. His experience in laboratory testing and biofilm control ensures the highest industry standards in water treatment processes and water management.Â
Additionally, his deep understanding of infrastructure and water data analysis provides long-term, cost-effective solutions that promote health and safety. His expertise ensures that businesses receive top-tier, quality water treatment solutions.
For insights into the latest industry trends, innovations, and best practices, explore the Complete Water Solutions Blog, where Nathan shares valuable information on water filtration systems, sustainability, and water solutions engineering. Â
Give Us A Call (855) 787-4200 or Email info@complete-water.com