What is Electroplating and How Does it Work?
Electroplating
Electroplating is a technique commonly used in the metal finishing industry to coat pieces of product in metal plating. Electroplating allows an engineer or manufacturer to combine the strength, electrical conductivity, abrasion resistance, corrosion resistance, and the appearance of the desired metal with different materials which have different benefits. These are materials such as metals or plastics that are affordable or lightweight.
To achieve this, engineers use the process of electrodeposition. This process is used to coat an object, or the base material, with a layer of metal, the metal with the desired qualities.Â
This process consists of using controlled electrolysis to transfer the metal coating from the anode, the metal plating, to the cathode, the base material. The anode and cathode are placed in the same electrolyte chemical bath. They are then exposed to continuous chemical charge. The electricity will cause the negatively charged ions, or anions, to move to the anode while the positively charged ions, cations, to transfer to the cathode. This transfer will cover the base material in the metal plating, therefore finishing the process of electroplating.
Materials
Electroplating commonly uses a lighter and/or lower-cost substrate material and plates it in a thin shell of metal. This substrate material is most commonly other metals. This is due to one basic requirement it must have. The substrate material must be conductive for the process to work.Â
Electroplating can be done by coating with one metal or a combined variety of metals. Some examples of the most common plating materials are:
- Brass
- Cadmium
- Copper
- Gold
- Iron
- Nickel
- Silver
- Titanium
- Zinc
Substrates, on the other hand, can be made of almost any material. Metals such as stainless steel are used more often due to its conductive nature, but any material can be used as long as it is made conductive first.
Benefits
Electroplating boasts many benefits to the engineers and manufacturers who use it. The main benefit is strength and durability. Engineers and manufacturers plate the substrate in a thin layer of metal to add to its strength and durability. By adding a thin layer of metal to a base material and its resistance to environmental factors such as chemical exposure or outdoor or corrosive applications.
Electroplating can also be used in aesthetic applications. The process is commonly used to add cosmetic finishes to consumer products. In the medical community electroplating is also used to make implants that are strong, corrosion-resistant, and can be easily and properly sterilized.
Electroplating can also increase the conductivity of a base substrate. Adding high-quality metal plating to a cheaper metal substrate can add to its conductivity and allow it to perform better in applications such as electrical components.
Limitations
The process of electroplating has many benefits but also has certain limitations. These lie in the complexity of the process itself. The process is highly technical and can be hazardous. Workers can unintentionally suffer from illnesses if the proper precautions are not taken. This includes having a properly vented workspace along with the proper components for the process.
Components
Any great process starts with a strong base component. In the case of electroplating that component is water. The metal-finishing industry commonly uses ultra-pure water to create the electrolyte solution used in electroplating.
This high-quality, ultra-pure water must be deionized. Deionized water contains very few ions aside from H20. This ensures that the electrolyte solution only contains what the engineers or manufacturers need to begin the electroplating process.
The water must also be completely clean and purified to allow the metal plating to be free of blemishes such as water spots. A bath of purified water after the electroplating will allow the engineer or manufacturer to test to make sure they are using the best water available.
Electroplating Water Systems
Electroplating water systems are used to ensure the water used in the process meets the specifications of each individual project. This can be achieved using a two-bed deionizer or reverse osmosis system. Both of these are available from your trusted water system supplier, Complete Water Solutions.
Here at Complete Water Solutions we also understand the issue of wastewater resulting from the process of electroplating. A wastewater treatment system is essential in dealing with the wastewater produced from electroplating. The wastewater can contain heavy metals, oils, and other toxins that can be damaging to the environment.Â
Complete Water can help with choosing the right source water treatment systems as according to engineer or manufacturer specifications and wastewater treatment systems as according to environmental regulations. Contact us today to get started on ensuring your electroplating system uses the best water possible and disposes of its wastewater properly!Â
Trust Complete Water Solutions to provide electroplating water systems and services.
Learn More About Electroplating & Contact Us!
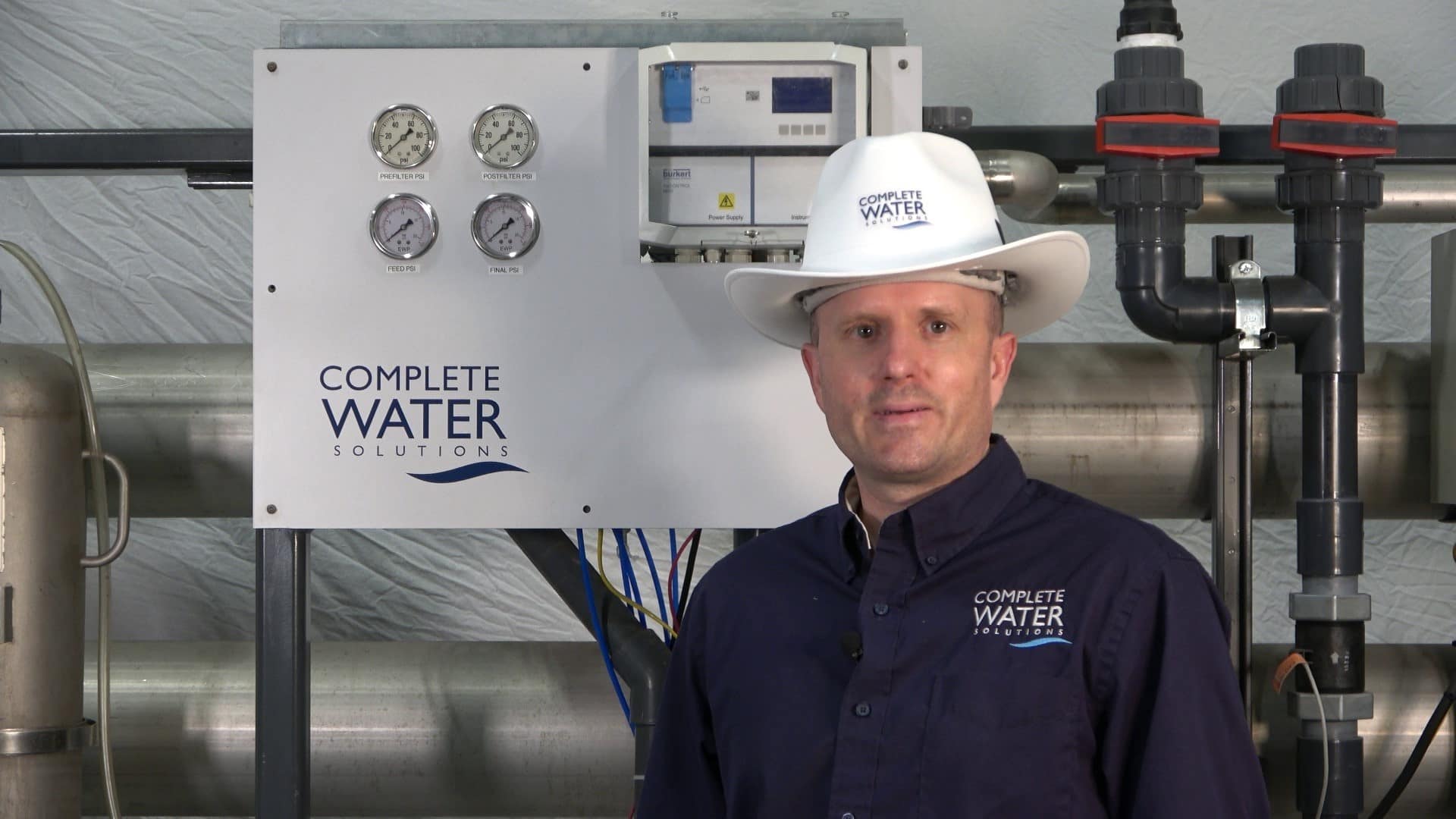
With over 30 years of hands-on experience in the water treatment industry, Nathan Olszak is a trusted water treatment expert. He specializes in designing, engineering, and servicing water treatment systems. As the owner of Complete Water Solutions, Osmonics, and Membrane Cleaning Pro, Nathan has built a reputation for delivering customized water treatment solutions that enhance efficiency, reliability, and water quality across various industries, including the medical, commercial, and manufacturing sectors.
Nathan’s journey in water treatment began as a service technician. He gained in-depth knowledge by working with all major brands of equipment, including Veolia, Suez, Bruner, Culligan, Pentair, Aquamatic, Osmonics, GE Water, Marlo, Lakeside, Fleck, Autotrol, US Filter, ION Pure, Siemens, Evoqua, and many others. This hands-on expertise, combined with his technical certifications, has made him a leader in water system engineering and water management.
Credentials & Expertise
- Certifications: David H. Paul Reverse Osmosis Certification, PLC Programming
- License: Power Plant Operating Engineer 3rd Class
- Specialties:
- Design & engineering of water treatment systems and advanced water systems
- Custom water filtration systems and solutions
- Installation, automation, and repair of water treatment systems
- Expertise in Reverse Osmosis (RO), Deionization, Water Softening, Carbon Filtration, Iron Filtration, UV Treatment, Ultrafiltration (UF), Process Filtration, CEDI/EDI, and more
- Specialized knowledge in Boiler Feed Water, Tower Makeup Water, and drinking water production for industries such as bottling, pharmaceuticals, and food processing
- Project management and reclaiming of water system waste for other uses
- Evaluation of raw water sources and potential contamination risks
- Industrial water treatment strategies to prevent corrosion and optimize system performance
- Boiler water treatment to enhance energy efficiency and system longevity
Nathan’s commitment to excellence extends beyond equipment sales and service. He works closely with clients to develop tailored water treatment services that optimize performance and meet their operations’ unique demands. His expertise covers methods that mitigate water impurities, ensure fresh water accessibility, and maintain regulatory compliance. It also includes the design of high-efficiency reverse osmosis systems for industrial use.
Nathan focuses on the latest technology in water conditioning, water softeners, filters, and pumps to improve maintenance and efficiency. His experience in laboratory testing and biofilm control ensures the highest industry standards in water treatment processes and water management.Â
Additionally, his deep understanding of infrastructure and water data analysis provides long-term, cost-effective solutions that promote health and safety. His expertise ensures that businesses receive top-tier, quality water treatment solutions.
For insights into the latest industry trends, innovations, and best practices, explore the Complete Water Solutions Blog, where Nathan shares valuable information on water filtration systems, sustainability, and water solutions engineering. Â
Give Us A Call (855) 787-4200 or Email info@complete-water.com