Industrial RO Membrane Foulants & How to Clean Them
Reverse Osmosis (RO) is an integral piece of technology in the industrial sector for purifying water to meet specific quality requirements. It is particularly useful in applications where high-quality water is crucial, such as in the pharmaceutical, food, and beverage industries. However, like any other equipment, RO systems can be negatively affected by fouling, which can lead to reduced water flow rates, increased energy consumption, decreased water production rates, and poor water quality.Â
What does this mean for you and your company? To put it simply, fouling is BAD! Therefore, it is essential to understand the causes of fouling and take steps to prevent and effectively clean fouling when it occurs. The experts at Complete Water Solutions can explain more about industrial RO membrane foulants and how to clean them.
What is Fouling and Why Should You Clean It?
Fouling is a process during which the continuous buildup of unwanted substances or particles reduces the function and efficiency of the operating system. This typically occurs on membrane systems, which are mechanical and therefore subject to high amounts of fouling on their surfaces. This fouling ultimately degrades the membranes, which if left for too long can be irreversible. If the fouling is left unaddressed and this happens, it can lead to costly equipment damage, increased downtime for maintenance, and ultimately shorten the lifespan of the entire system. No company wants to or should have to deal with these issues, and luckily, dangerous levels of fouling are preventable. With the help of experts, like those at Complete Water Solutions, fouling can be removed to help maintain your equipment so you can go about business as usual.
What Causes Fouling?
Fouling can be different for every different company based on a number of factors. It is important to know the cause of fouling on your equipment so you can get it properly cleaned and make adjustments to prevent fouling in the future. Wondering what might be causing your fouling?
- Oxidation: Chlorine, chloramines, ozone, hydrogen peroxide, and other chemicals are oxidizers that have the ability to attack the structure of the membrane’s concentrate layer. This does differing amounts of damage to the different parts of your equipment. The odds of this happening are increased if metals such as iron and copper are used in the feed in the water because they increase the rate of oxidation. If this oxidation is extensive, then salt rejection will drop and at a certain point, the cost of running your equipment will skyrocket.Â
- Suspended Solids: Suspended solids in the feedwater to your machines deposit on the membrane surface. This blocks feed channels and can especially cause problems for a system’s lead membranes. Silt, clay, silica, iron, manganese, and aluminum are some of the suspended solids that may be causing this problem.
- Scaling: Substances such as calcium, barium, strontium silica, and other salts can become super saturated at the surface of a membrane, reducing the amount of water that can pass through the feed channel and permeate through the membrane.Â
- Organic: Naturally occurring organics found in surface water can also cause fouling. Additional materials that may cause organic fouling can be coagulants (or flocking agents) and incompatible pretreatment chemicals.Â
- pH Extremes: Hydrolysis is a chemical change that decomposes the membrane and can be caused by extremes in pH balance. A membrane’s thin film composite layer will operate at a pH level of 2-11, but the membrane’s pH range is only from 5-8. If the level reaches outside this range, hydrolysis occurs which will cause your machine’s membrane to perform poorly.Â
- Biological: Biological material, like organic slimes and bacteria, can also grow on the surface of a membrane, reducing the feed channel and permeate flows.Â
- Temperature: When temperature limits are exceeded, thermal damage occurs for the membrane, leaving it generally useless. It is important to be aware of the maximum temperature limit for the machines you are using specifically. The maximum temperature limit for cellulose acetate membranes is 35 degrees Celsius, and for most thin film composites, the temperature maximum is 45 degrees Celsius. After the temperature exceeds this, the membrane is a total loss.
That’s a lot of information to take in, but staying informed on what might be causing the inefficiencies in your machines is the first step to making improvements.Â
How To Clean Foulants?
Each type of fouling has a different cleaning process, and many times, foulants will pile on top of one another meaning a combined strategy is needed to help get your machines back to pristine condition. To figure out the best method of cleaning, a two-step process can be used to identify all of the foulants on your equipment. First, profiling involves using the sample ports for each vessel to check the water’s conductivity and pressure drop. They are then compared to one another and if one has a higher conductivity than the other, a probing of that vessel will take place. This process isolates the problem within the vessel without removing the elements and while the system is still online. From this data, you are able to determine whether the first or second stage is fouled.Â
After that, it’s finally time to clean your machines and get them back in tip-top shape!
If your fouling has been determined to be biological or organic, the bacteria and organics can be removed by soaking the machine with a high pH substance and at a high temperature. This process can be done in as few as 2 hours of soaking, but for best results, it will take between 12 and 13 hours. After that has been removed, if there are inorganic salts, they are targeted next. Equipment will be soaked in a low-pH cleaner or Hydrochloric acid until the membrane is clean. Finally, if there is particulate fouling, it can be freed up and removed. This procedure is aggressive, so off-site cleaning is highly recommended.Â
As you can see, there are a lot of technicalities that come along with identifying Industrial RO Membrane Foulants and their cleaning, which is why you should always choose an expert to help you restore your machines. Complete Water Solutions is the industry leader in removing fouling and will help guide you through every step of the complex process, from identifying the foulant to cleaning it up. Contact us today with any questions or to schedule a cleaning.Â
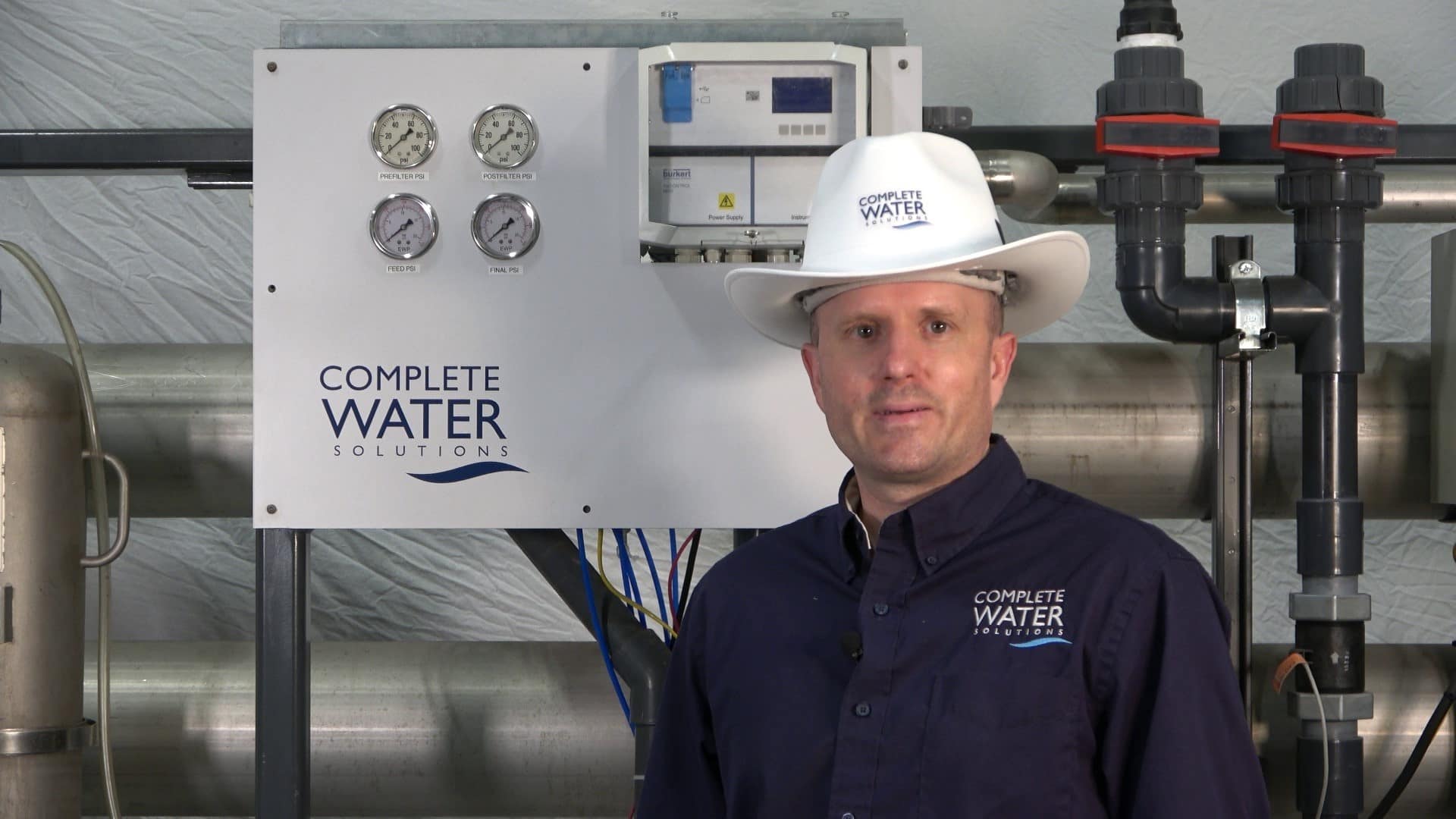
With over 30 years of hands-on experience in the water treatment industry, Nathan Olszak is a trusted water treatment expert. He specializes in designing, engineering, and servicing water treatment systems. As the owner of Complete Water Solutions, Osmonics, and Membrane Cleaning Pro, Nathan has built a reputation for delivering customized water treatment solutions that enhance efficiency, reliability, and water quality across various industries, including the medical, commercial, and manufacturing sectors.
Nathan’s journey in water treatment began as a service technician. He gained in-depth knowledge by working with all major brands of equipment, including Veolia, Suez, Bruner, Culligan, Pentair, Aquamatic, Osmonics, GE Water, Marlo, Lakeside, Fleck, Autotrol, US Filter, ION Pure, Siemens, Evoqua, and many others. This hands-on expertise, combined with his technical certifications, has made him a leader in water system engineering and water management.
Credentials & Expertise
- Certifications: David H. Paul Reverse Osmosis Certification, PLC Programming
- License: Power Plant Operating Engineer 3rd Class
- Specialties:
- Design & engineering of water treatment systems and advanced water systems
- Custom water filtration systems and solutions
- Installation, automation, and repair of water treatment systems
- Expertise in Reverse Osmosis (RO), Deionization, Water Softening, Carbon Filtration, Iron Filtration, UV Treatment, Ultrafiltration (UF), Process Filtration, CEDI/EDI, and more
- Specialized knowledge in Boiler Feed Water, Tower Makeup Water, and drinking water production for industries such as bottling, pharmaceuticals, and food processing
- Project management and reclaiming of water system waste for other uses
- Evaluation of raw water sources and potential contamination risks
- Industrial water treatment strategies to prevent corrosion and optimize system performance
- Boiler water treatment to enhance energy efficiency and system longevity
Nathan’s commitment to excellence extends beyond equipment sales and service. He works closely with clients to develop tailored water treatment services that optimize performance and meet their operations’ unique demands. His expertise covers methods that mitigate water impurities, ensure fresh water accessibility, and maintain regulatory compliance. It also includes the design of high-efficiency reverse osmosis systems for industrial use.
Nathan focuses on the latest technology in water conditioning, water softeners, filters, and pumps to improve maintenance and efficiency. His experience in laboratory testing and biofilm control ensures the highest industry standards in water treatment processes and water management.Â
Additionally, his deep understanding of infrastructure and water data analysis provides long-term, cost-effective solutions that promote health and safety. His expertise ensures that businesses receive top-tier, quality water treatment solutions.
For insights into the latest industry trends, innovations, and best practices, explore the Complete Water Solutions Blog, where Nathan shares valuable information on water filtration systems, sustainability, and water solutions engineering. Â
Give Us A Call (855) 787-4200 or Email info@complete-water.com