How to Record Your RO System’s Performance
RO Systems can be simple and complex and used in various applications. It’s essential to know how to record your RO system’s performance. In this blog, we are going to just be focusing on RO Systems for water treatment applications and how to make sure they’re running at their best! We get quite a few questions when it comes to Reverse Osmosis Equipment. But some of the most common questions we receive are:
- What Testing Should We Be Doing On Our RO System?
- What Pressures Should My RO Be Running At?
- What Are My Flow Rates?
- What Do We Need To Do  & When Do We Need To Do It?
RO System Maintenance
All RO Systems will require maintenance at some point from pre-filter changes to membrane cleanings and much more. Every water source is different and because of this, the required maintenance schedule will differ from location to location. Â Even how the system is designed can change how and when maintenance is performed. It can even change how often you clean your RO Membranes including what chemistry you use. In order to begin to lay out a plan, it first starts with monitoring your system and that starts with a Reverse Osmosis Daily Log. This daily RO log should be filled out daily to help you trend the performance of the RO System. By trending this data you can begin to see trends that can begin laying out your maintenance routine.
In the example below, we look at Pre Filter Pressure Inlet & Post Filter Pressure.
Day 1 | Day 2 | Day 3 | Day 4 | Day 5 | |
Pre Filter PSI | 40 | 40 | 40 | 40 | 40 |
Post Filter PSI | 40 | 34 | 30 | 25 | 40 |
Filter DP | 0 | 6 | 10 | 15 | 0 |
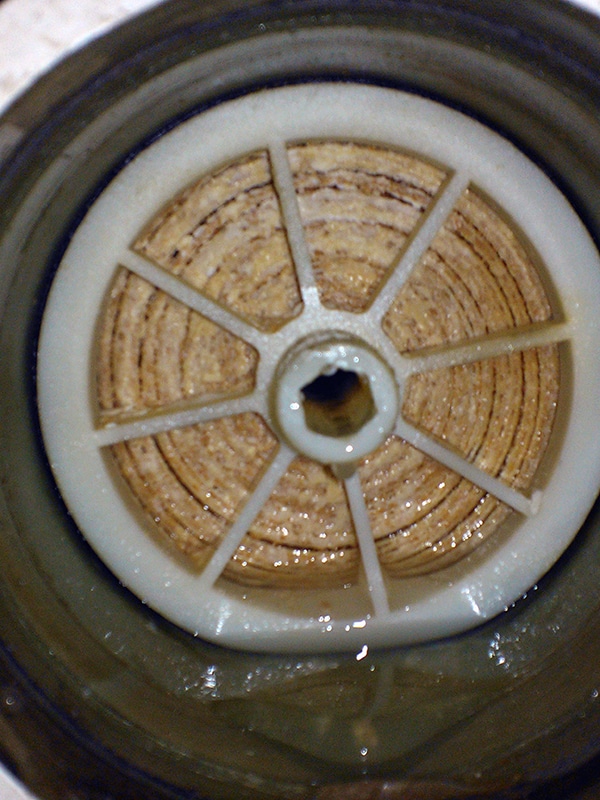
Irreversible Scaled RO Membrane
By recording the pre-filter inlet pressure and post pressure we are able to identify how often we need to change the Pre Filter. As seen in this example we change the pre-filter on Day 4 which had a 15-pound differential pressure. After changing the filter we went back to 0 psi differential pressure. If we continue to trend it we may find that every 4 days we need to change the pre-filter. This can then be logged as a maintenance item and now you can pre-plan for your time and products to be on hand. If you have to change 1 filter every 4 days you can calculate out how many you may need for the year to keep stock.
The other items that you may be logging on the RO Log Sheet can help with other items such as RO membrane cleanings or RO membrane replacement.
Many of the major membrane manufacturers agree on the following statements:
- Reverse Osmosis membranes should be cleaned when normalized flow decreases by 10% from the initial acceptance test conditions
- Reverse Osmosis membranes should be cleaned when the overall pressure drop increases by 15% over the initial acceptance test conditions.
These two simple, explicit statements often go ignored, despite the fact that it has been demonstrated that the optimum cleaning response is achieved when these guidelines are followed. It can be difficult to recover performance if the system operates in a fouled condition for an extended period of time. Operating in a fouled condition could also cause irreversible damage to the Reverse Osmosis Membrane, which would require costly membrane replacements.
Logging this data and setting up your maintenance plan can help keep your reverse osmosis system in good operating condition. We know how busy you are, so we created a simple daily form to help you record your RO system’s performance and keep it in top-performing capacity. Below is the link to download the Free RO Daily Log Sheet.
Free Reverse Osmosis Daily Log Form (click to download pdf)
If you want some more help learning how to record your RO system’s performance, we’d be happy to help! Contact Us!
(855) 787-4200 or info@complete-water.com
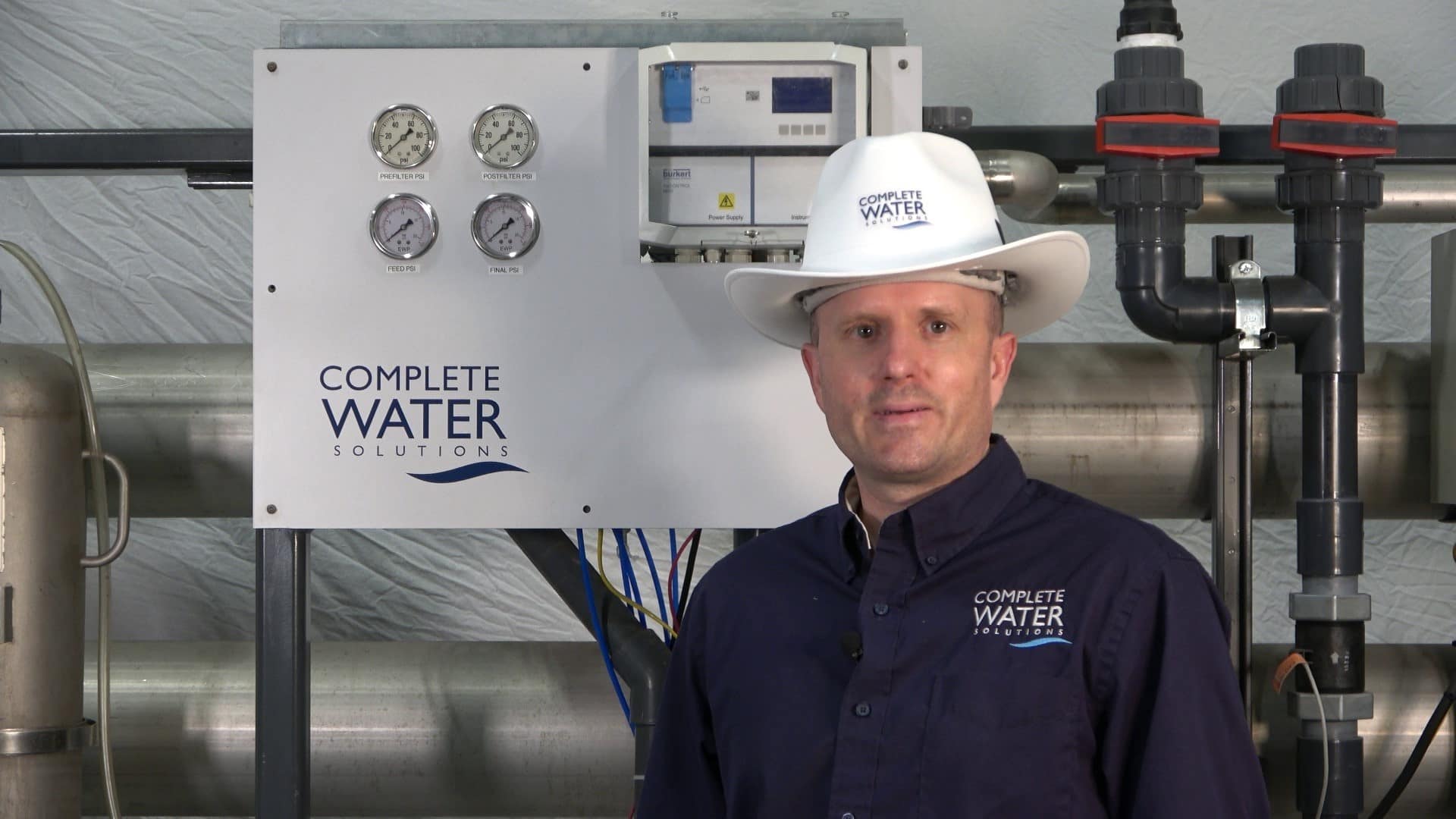
With over 30 years of hands-on experience in the water treatment industry, Nathan Olszak is a trusted water treatment expert. He specializes in designing, engineering, and servicing water treatment systems. As the owner of Complete Water Solutions, Osmonics, and Membrane Cleaning Pro, Nathan has built a reputation for delivering customized water treatment solutions that enhance efficiency, reliability, and water quality across various industries, including the medical, commercial, and manufacturing sectors.
Nathan’s journey in water treatment began as a service technician. He gained in-depth knowledge by working with all major brands of equipment, including Veolia, Suez, Bruner, Culligan, Pentair, Aquamatic, Osmonics, GE Water, Marlo, Lakeside, Fleck, Autotrol, US Filter, ION Pure, Siemens, Evoqua, and many others. This hands-on expertise, combined with his technical certifications, has made him a leader in water system engineering and water management.
Credentials & Expertise
- Certifications: David H. Paul Reverse Osmosis Certification, PLC Programming
- License: Power Plant Operating Engineer 3rd Class
- Specialties:
- Design & engineering of water treatment systems and advanced water systems
- Custom water filtration systems and solutions
- Installation, automation, and repair of water treatment systems
- Expertise in Reverse Osmosis (RO), Deionization, Water Softening, Carbon Filtration, Iron Filtration, UV Treatment, Ultrafiltration (UF), Process Filtration, CEDI/EDI, and more
- Specialized knowledge in Boiler Feed Water, Tower Makeup Water, and drinking water production for industries such as bottling, pharmaceuticals, and food processing
- Project management and reclaiming of water system waste for other uses
- Evaluation of raw water sources and potential contamination risks
- Industrial water treatment strategies to prevent corrosion and optimize system performance
- Boiler water treatment to enhance energy efficiency and system longevity
Nathan’s commitment to excellence extends beyond equipment sales and service. He works closely with clients to develop tailored water treatment services that optimize performance and meet their operations’ unique demands. His expertise covers methods that mitigate water impurities, ensure fresh water accessibility, and maintain regulatory compliance. It also includes the design of high-efficiency reverse osmosis systems for industrial use.
Nathan focuses on the latest technology in water conditioning, water softeners, filters, and pumps to improve maintenance and efficiency. His experience in laboratory testing and biofilm control ensures the highest industry standards in water treatment processes and water management.Â
Additionally, his deep understanding of infrastructure and water data analysis provides long-term, cost-effective solutions that promote health and safety. His expertise ensures that businesses receive top-tier, quality water treatment solutions.
For insights into the latest industry trends, innovations, and best practices, explore the Complete Water Solutions Blog, where Nathan shares valuable information on water filtration systems, sustainability, and water solutions engineering. Â
Give Us A Call (855) 787-4200 or Email info@complete-water.com