Beverage Reverse Osmosis Systems Maintenance & Compliance
Complete Water Solutions provides a wide array of services for Reverse Osmosis Systems and Equipment. Whether you purchased it from CWS or from another manufacture, we can provide a wide arrange of services. RO systems used for beverage ingredients and pharmaceuticals ingredients have a few things in common.
SOP’s / Compliance / Service
Some commonalities:
Using NSF Approved Materials -If you manufacture, sell or distribute water treatment or distribution products in North America, your products are required to comply with NSF/ANSI 61: Drinking Water System Components – Health Effects by most governmental agencies that regulate drinking water supplies. Developed by a team of scientists, industry experts and key industry stakeholders, NSF/ANSI 61 sets health effects criteria for many water system components including:
- Protective barrier materials (cement, paints, coatings)
- Joining and sealing materials (gaskets, adhesives, lubricants)
- Mechanical devices (water meters, valves, filters)
- Pipes and related products (pipe, hose, fittings)
- Plumbing devices (faucets, drinking fountains)
- Process media (filter media, ion exchange resins)
- Non-metallic potable water materials
http://www.nsf.org/services/by-industry/water-wastewater/municipal-water-treatment/nsf-ansi-standard-61
If you haven’t done so keeping a NSF Cert Book or Log book is a good idea. This helps with verifying and determining that all the products that have been used in your system comply with NSF 61.
Routine or Validated Service Cycle
Most water treatment equipment does not come with a service cycle or a service schedule. Many systems come with a “troubleshooting guide”. Water systems that are used for production should have a set service schedule. These service schedules are to help ensure the quality and safety of water used for production.
Items Included In Service Cycles
- Carbon Change – Changing out carbon beds
- UV Bulbs – Annual Changing Of UV Bulbs, Sleeves & Orings
- RO Pre Filter Changes – Monthly Or Sooner
- RO Membrane Cleaning – Quarterly
- RO Membrane Change Out – 3-5 Years
- Post Filter Change Out – 6 Months
- Cleaning Of Injection Quills Or Replacement – Annually
- Rebuild Chemical Feed Pumps – Annually
- Monitoring Equipment Calibration – Annually
- Rebuilding Of Pre-treatment Equipment – 3 – 5 years
These are just a few examples of some scheduled maintenance to be performed. All maintenance should be recorded and documented along with updating any lot numbers of materials used. Don’t forget to update your NSF Certs at this time should you have changed the product being used.
If you need assistance with SOP’s / Validating or Setting a Service Schedule – Contact Complete Water Solutions
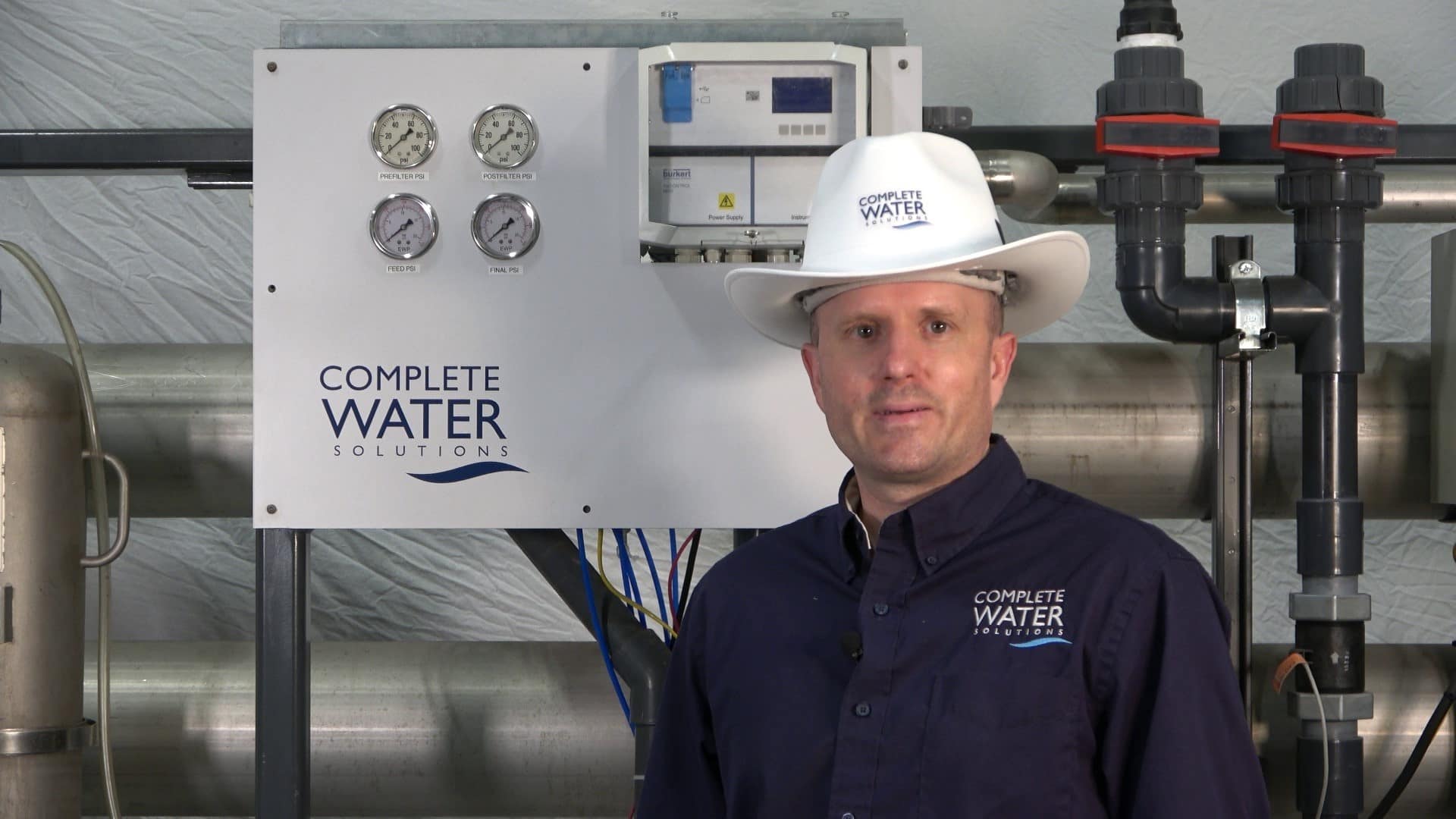
With over 30 years of hands-on experience in the water treatment industry, Nathan Olszak is a trusted water treatment expert. He specializes in designing, engineering, and servicing water treatment systems. As the owner of Complete Water Solutions, Osmonics, and Membrane Cleaning Pro, Nathan has built a reputation for delivering customized water treatment solutions that enhance efficiency, reliability, and water quality across various industries, including the medical, commercial, and manufacturing sectors.
Nathan’s journey in water treatment began as a service technician. He gained in-depth knowledge by working with all major brands of equipment, including Veolia, Suez, Bruner, Culligan, Pentair, Aquamatic, Osmonics, GE Water, Marlo, Lakeside, Fleck, Autotrol, US Filter, ION Pure, Siemens, Evoqua, and many others. This hands-on expertise, combined with his technical certifications, has made him a leader in water system engineering and water management.
Credentials & Expertise
- Certifications: David H. Paul Reverse Osmosis Certification, PLC Programming
- License: Power Plant Operating Engineer 3rd Class
- Specialties:
- Design & engineering of water treatment systems and advanced water systems
- Custom water filtration systems and solutions
- Installation, automation, and repair of water treatment systems
- Expertise in Reverse Osmosis (RO), Deionization, Water Softening, Carbon Filtration, Iron Filtration, UV Treatment, Ultrafiltration (UF), Process Filtration, CEDI/EDI, and more
- Specialized knowledge in Boiler Feed Water, Tower Makeup Water, and drinking water production for industries such as bottling, pharmaceuticals, and food processing
- Project management and reclaiming of water system waste for other uses
- Evaluation of raw water sources and potential contamination risks
- Industrial water treatment strategies to prevent corrosion and optimize system performance
- Boiler water treatment to enhance energy efficiency and system longevity
Nathan’s commitment to excellence extends beyond equipment sales and service. He works closely with clients to develop tailored water treatment services that optimize performance and meet their operations’ unique demands. His expertise covers methods that mitigate water impurities, ensure fresh water accessibility, and maintain regulatory compliance. It also includes the design of high-efficiency reverse osmosis systems for industrial use.
Nathan focuses on the latest technology in water conditioning, water softeners, filters, and pumps to improve maintenance and efficiency. His experience in laboratory testing and biofilm control ensures the highest industry standards in water treatment processes and water management.
Additionally, his deep understanding of infrastructure and water data analysis provides long-term, cost-effective solutions that promote health and safety. His expertise ensures that businesses receive top-tier, quality water treatment solutions.
For insights into the latest industry trends, innovations, and best practices, explore the Complete Water Solutions Blog, where Nathan shares valuable information on water filtration systems, sustainability, and water solutions engineering.
Give Us A Call (855) 787-4200 or Email info@complete-water.com