How Often Should Industrial Water Systems Be Serviced?
Water systems are the lifeline of daily operations in industrial settings. Having a water system that is running smoothly is crucial to maintaining a productive industrial business. You want to ensure your system runs efficiently to improve your productivity, stay in compliance with safety and health regulations, and reduce the costs of your operation. The best way to ensure this is to conduct regular servicing and maintenance on your industrial water system.
There are a number of reasons why it is important to have your water system serviced, and most of these reasons are true across different industries. One of the biggest reasons is to keep your water supply safe. Having unsafe water can lead to unsafe conditions for your employees. Not only that, but depending on the industry you work in, it can also directly affect your clients and customers negatively.Â
No one likes having to replace water systems, as it can be costly. Maintaining the life span of your water system is just another one of the many reasons why you should have your water system serviced. Not only is it expensive to replace an entire system, but regular maintenance can save you money in the long run by avoiding potential breakdowns. A little bit of maintenance will help keep your system functioning and costing you less in the long run. Consider what materials you’re using in your water system. The quality of the system’s design is also an important factor in the life span of your water system. Storage of your water system also plays a role in the system’s lifespan. If stored incorrectly, this can negatively affect its performance and cost you money. Don’t let these reasons ruin your company’s productivity.
The easiest way to prevent any complications with your water system is by scheduling preventative maintenance. Having a set routine can help you avoid equipment failure. There are a number of ways to conduct maintenance, but it is pivotal to the success of taking care of the system. Different tasks, like replacing a filter on a RO water system once a month, can be nailed down by trial and error during your maintenance. Also, make sure to consider maintaining your water systems based on how much you use the system. Use different meters or metrics to monitor how much the system is being used. Use this information to determine when to complete a task, like running a clean-in-place cycle every 2 million gallons of water being treated in an ultrafiltration system.
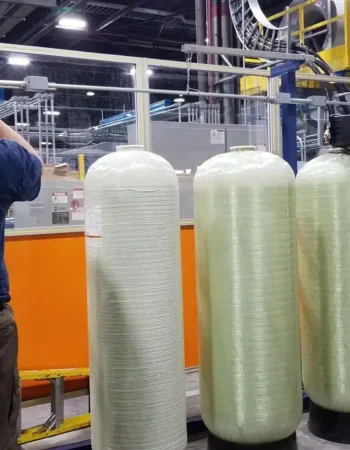
Repairs and replacements are also important. If you have a part that isn’t working properly, this can prevent the filtration system from correctly filtering the water or even prevent the system from working at all. Clean and test parts of your system regularly to ensure that they are working properly. If not, replace them to ensure the machine is functioning correctly.
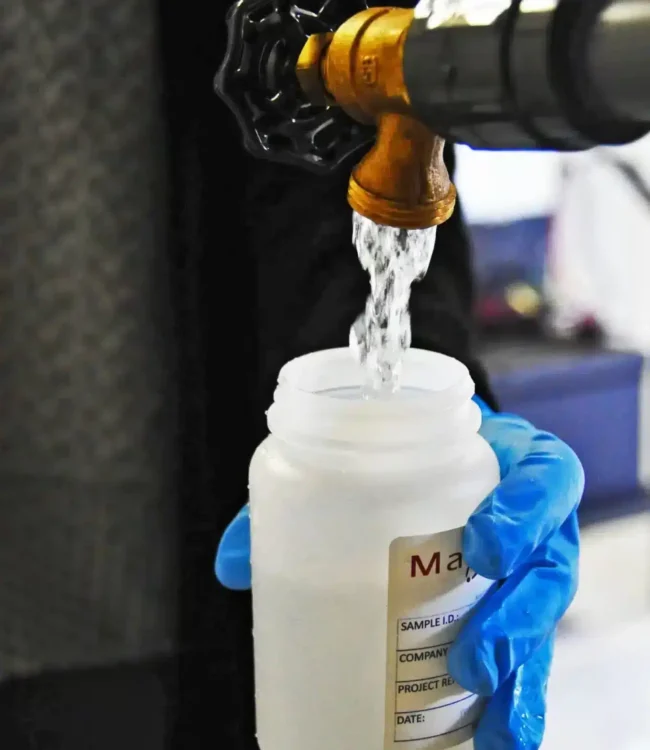
How Often Should I Service My Water System
If you’re unsure of how often you should service your water system, below are some guidelines on how often you should conduct maintenance. When you are using your water system a lot, monthly inspections for basic maintenance are a must. Wear and tear are inevitable on a machine, but the more you use it, the more prone to needing a part to be replaced. That also means that annual deep servicing and refurbishing are also important. Whether you’re using the system all the time or a couple of times a month, you should still check the system in depth once a year. During this yearly check, do a deep clean on your water system and see if any parts need refurbishment.Â
Some maintenance is also dependent on how old the system is. Newer systems (hopefully) won’t need to be refurbished or need any parts replaced for a while. If you’re operating with an older water system, chances are there might be parts that need replacing or even full refurbishment. Following the monthly and annual maintenance checks will help prevent this, but older systems may need more attention. The industry you’re working in can also affect how often you should perform maintenance on your water system. Health care water systems are more focused on controlling infections and patient safety, whereas food processing industries are more focused on protecting public health. The way these systems run is drastically different, and the amount of time they spend running differs as well. Testing and maintaining these systems will differ for these reasons. Overall, make sure to stay compliant with codes within your industry as well as local and federal regulations and codes.
Trust Complete Water Solutions to Help Service Your Industrial Water System
Maintaining your water system isn’t an option – it’s a necessity. Whether wanting to boost productivity or ensure safe water, regular servicing of your industrial water system is the best practice to adhere to. Knowing the importance of maintenance will ensure safe, efficient, and long-lasting water systems. If you don’t know where to begin with servicing your industrial water system, reach out to our team at Complete Water Solutions. We’re experts in water filters and systems, and we would love to help you with yours!
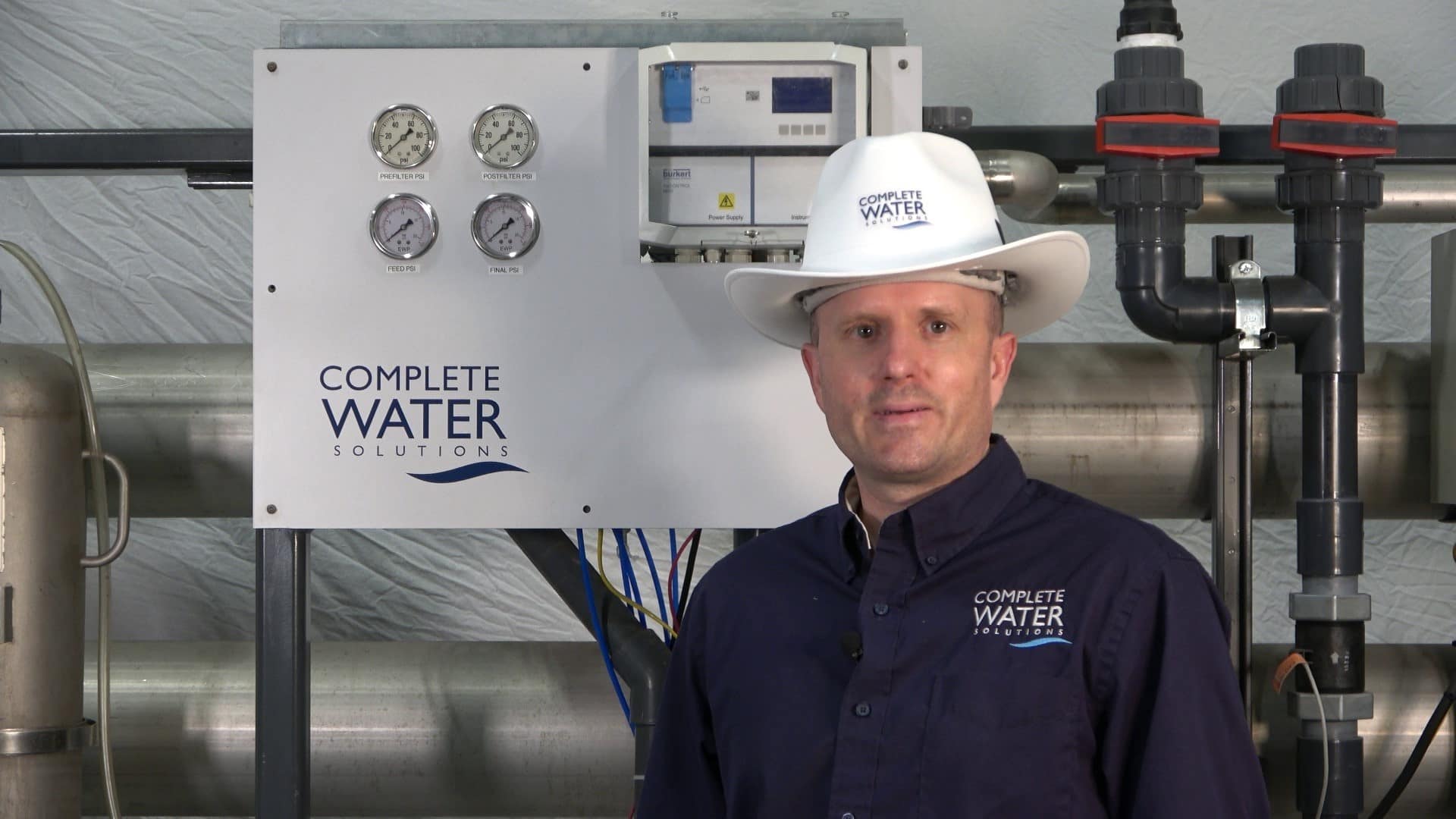
With over 30 years of hands-on experience in the water treatment industry, Nathan Olszak is a trusted water treatment expert. He specializes in designing, engineering, and servicing water treatment systems. As the owner of Complete Water Solutions, Osmonics, and Membrane Cleaning Pro, Nathan has built a reputation for delivering customized water treatment solutions that enhance efficiency, reliability, and water quality across various industries, including the medical, commercial, and manufacturing sectors.
Nathan’s journey in water treatment began as a service technician. He gained in-depth knowledge by working with all major brands of equipment, including Veolia, Suez, Bruner, Culligan, Pentair, Aquamatic, Osmonics, GE Water, Marlo, Lakeside, Fleck, Autotrol, US Filter, ION Pure, Siemens, Evoqua, and many others. This hands-on expertise, combined with his technical certifications, has made him a leader in water system engineering and water management.
Credentials & Expertise
- Certifications: David H. Paul Reverse Osmosis Certification, PLC Programming
- License: Power Plant Operating Engineer 3rd Class
- Specialties:
- Design & engineering of water treatment systems and advanced water systems
- Custom water filtration systems and solutions
- Installation, automation, and repair of water treatment systems
- Expertise in Reverse Osmosis (RO), Deionization, Water Softening, Carbon Filtration, Iron Filtration, UV Treatment, Ultrafiltration (UF), Process Filtration, CEDI/EDI, and more
- Specialized knowledge in Boiler Feed Water, Tower Makeup Water, and drinking water production for industries such as bottling, pharmaceuticals, and food processing
- Project management and reclaiming of water system waste for other uses
- Evaluation of raw water sources and potential contamination risks
- Industrial water treatment strategies to prevent corrosion and optimize system performance
- Boiler water treatment to enhance energy efficiency and system longevity
Nathan’s commitment to excellence extends beyond equipment sales and service. He works closely with clients to develop tailored water treatment services that optimize performance and meet their operations’ unique demands. His expertise covers methods that mitigate water impurities, ensure fresh water accessibility, and maintain regulatory compliance. It also includes the design of high-efficiency reverse osmosis systems for industrial use.
Nathan focuses on the latest technology in water conditioning, water softeners, filters, and pumps to improve maintenance and efficiency. His experience in laboratory testing and biofilm control ensures the highest industry standards in water treatment processes and water management.Â
Additionally, his deep understanding of infrastructure and water data analysis provides long-term, cost-effective solutions that promote health and safety. His expertise ensures that businesses receive top-tier, quality water treatment solutions.
For insights into the latest industry trends, innovations, and best practices, explore the Complete Water Solutions Blog, where Nathan shares valuable information on water filtration systems, sustainability, and water solutions engineering. Â
Give Us A Call (855) 787-4200 or Email info@complete-water.com