Control of Odors in the Brewing & Food Processing Industries – Part 3
Control of Odors in the Brewing &
Food Processing Industries - Part 3
Previously, we discussed the problems with odors that often emanate from breweries and food processing plants as well as learning more about hydrogen sulfide, the common cause of these odor problems. Below, we discuss programs and solutions that can be used to control these odors dependent on the needs of your plant.
Programs & Solutions to Control Odors
At least four chemical means of controlling odors are generally used in the industrial setting:
- Organic Scavenging – Primary amines
- Chemical Oxidation – Chlorination, hydrogen peroxide, permanganate, ozone
- Precipitation – Iron salts
- Control by pH – Lime, soda caustic
Other Solutions:
- Selective organic scavenger
- Biomodifiers – nitrates and proprietary inhibitors
- Masking agents
- Neutralizers
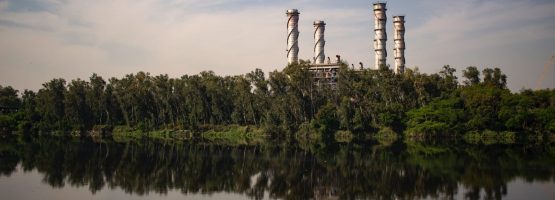
Biomodifiers
Biomodifiers such as nitrate can be used in anaerobic and facultative lagoons to aid in controlling odors with some success. Anaerobic bacteria use nitrate in preference to sulfate as an electron acceptor during the metabolism of organic substances. When nitrate is present, sulfide-producing bacteria will choose it over sulfate that may be present. This results in a byproduct of their activity that becomes odorless nitrogen rather than objectionable H₂S. Some of the disadvantages of using nitrates (biomodifiers) are the necessity of significant contact time in order for proper utilization to occur as well as a limitation in effluent waterways.
Precipitation
Metal salts such as ferric chloride react as follows and precipitate the sulfide from water as ferric sulfide salts. In addition to sludge formation, handling of the iron salts presents a corrosion problem all of its own.
2FeCl₂ + 3H₂S → Fe₂S₃↓ + 6HCl
Neutralizers
Neutralizers function in a complex manner. This is because of the makeup of the neutralizers. Those neutralizers that contain essential oils primarily function by capturing odor molecules in a charge film that surrounds the essential oil-water complex. Neutralizers that contain other large organic molecules created by certain fermentation and blending processes function by absorbing odor molecules, by radical reaction, or by condensation reaction between the odor molecules and the neutralizer.
Oftentimes, the latter compounds produce a neutralizer reaction product that does not create or leave a detectable odor. Within the neutralizer grouping, the essential oils tend to control a wider range of odors. However, there may be a detectable odor of the essential oil present after odor neutralization.
Organic Scavenging
Organic scavengers are typically comprised of primary amines that react with reduced sulfur compounds that have acidic protons, as shown in the figure below:
H2S ↔ HS⁻ +; H⁺; HS⁻ ↔S= + H₊
The benefits of using an organic scavenger include:
- Ease of handling and simple feed equipment
- No pH change
- No sludge generation
Selective organic scavenging is also available through other chemical compounds available from some distributors that can increase the efficiency of the process as well.
Masking Agents
Masking agents have been viewed in a negative light in more recent years. Primarily, this negativity stems from the fact that in order to mask an odor, the masking agent must create a stronger odor. If this option is used, there is often a perception that something is being hidden. The masking of odors can prevent a severe health risk when H₂S is being masked. Masking does not mitigate the health risks!
Chemical Oxidizers
Oxidizers such as chlorine donating material have safety and handling problems. Furthermore, chlorine donors may contribute to the formation of carcinogenic trihalomethanes (THM), and thus chlorine as an oxidation agent is not recommended in most cases.
Hydrogen peroxide oxidizes H₂S and, depending upon the pH of the water system, will yield different products as shown below:
pH < 8.5 H₂O₂ + H₂S → S + 2H₂O
pH > 8.5 4H₂O₂ + S⁻² → SO4⁻² + 4H₂O
At pH < 8.5, the stoichiometric H₂O₂ requirement is 1 gram H₂O₂ for each 1 gram of H₂S. In actual use, however, more H₂O₂ is required because H₂O₂ is not selective in what it attacks and therefore oxidizes other materials and organic matter in addition to H₂S. Many oxidizers have similar usage characteristics to that of H₂O₂ .
At Complete Water Solutions, we have been successful in treating an array of problematic odors that commonly occur in the brewing and food processing industries. To find the best solution for your brewery or food processing plant, contact Complete Water Solutions today!