Types of Boiler System Failures
Common Types of Boiler System Failures
Deaerator Cracking
One of the more common types of boiler system failures is deaerator cracking. In several deaerators, cracks can develop at welds and in heat-affected areas near the welds. Most often, this occurs at the head-to-shell weld below the water level in the storage compartment. It can also happen above the water level or at longitudinal welds. Due to cracks developing at the point of equipment malfunction, they can cause a potential safety hazard. Which then would require periodic inspection of equipment and/or replacement and repair. To identify cracks, we suggest testing with wet fluorescent magnetic particles.
The instrument of numerous deaerator cracking has been determined as environmentally assisted fatigue cracking. However, exact reasons are unknown, processes can be taken to reduce the potential for cracking. Some suggestions include, minimizing thermal and mechanical stress during operation and relieving stress on the welds. Water chemistry should also be composed to lessen corrosion.
Feedwater Line Erosion
Another more common of the types of boiler system failures is from feedwater line erosion. High-velocity water and notably water/steam mixtures cause erosion in feedwater systems. Most frequently encountered erosion problems appear at the hairpin bends in streaming economizers. On this spot, the concoction of water and steam thins the elbows, leaving a distinctive reverse horseshoe imprint.
Problems can also occur in feedwater lines where high velocities create the familiar thinning pattern. Problems can also be experienced at moderate average flow speeds when an arrangement of bends cause a significant advancement in local velocity. Keeping water chemistry conditions at the most tenacious oxide layers will be helpful in reducing erosion problems. Nonetheless, these problems will not be fully fixed unless an operational or design change occurs.
Economizer Boiler Tube Failure
Water tube economizers are oftentimes exposed to the serious damage of oxygen pitting. The harshest damage occurs at the economizer inlet and at the tube weld seams. Where economizers are installed, effective deaerating heater operation is unquestionably imperative. The application of a fast-acting oxygen hunter, like catalyzed sodium sulfite, also helps protect this crucial part of the boiler.
While oxygen pitting is the most frequent form of waterside corrosion that causes economizer tube failures, caustic soda will sometimes accumulate under deposits and caused abrasive gouging. This type of attack can develop in an area of an economizer where steam formation is taking place under a deposit and free caustic soda is present in the feedwater. The best result to this type of boiler system failure is improved treatment that will eliminate the deposition.
Other typical reasons of economizer failure consist of fatigue cracking at the rolled tube ends and fireside decay generate from the condensation of acid coming out of the boiler flue gas.
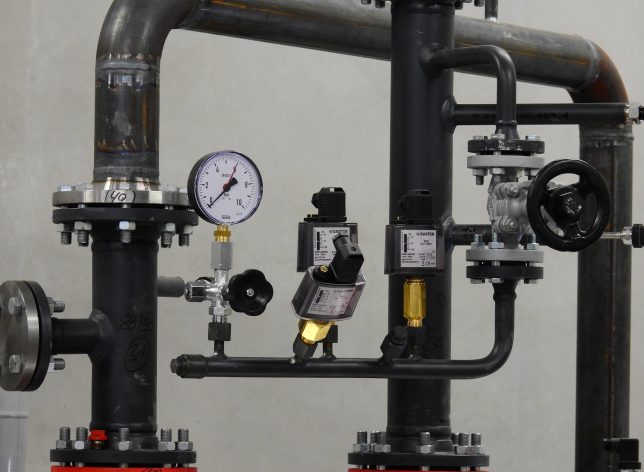
Boiler Failures Due To Overheating
Overheating is yet another of the most common types of boiler water system failures and one of the leading causes of downtime. When tube failures happen because of overheating and plastic flow, the reason is typically identified by the deposits which remain. An accurate inquiry of the deposits indicates the origin of the problem and the procedure needed for correction. Metallographic analyses are helpful in deciding whether a short- or long-term exposure to overheating conditions endured before the failure. Such analyses are useful when metal quality or manufacturing shortcomings are speculated. However, these factors are important only in isolated occurrences.
When tube failures in boiler systems occur due to overheating, a careful examination of the failed tube section will show whether the failure is due to quick escalation in tube wall temperature or a long-term, steady buildup of deposit. The steady buildup of deposits can increase your utility costs, and cause high temperatures. When conditions cause an accelerated elevation in metal temperature to 1600°F or above, plastic flow settings are reached and a violent burst occurs. Ruptures indicated by thin, sharp edges are identified as “thin-lipped” bursts.
Violent bursts of the thin-lipped variety occur when water circulation in the tube is disrupted by blockage or by current failure caused by low water levels. In some steam drum designs, water level is absolutely critical because the baffling could isolate a generating location of the boiler when the steam drum water level drop below a certain mark.
Thin-lipped bursts can also happen in superheater tubes if steam flow is inadequate, if deposits restrict flow, or if tubes are closed off by water due to a quick firing rate during boiler start-up.
Disturbances in flow do not always conclude in rapid failure. Depending on the metal temperature occurred, the tube can be injured by corrosive or thinning mechanisms over an extended period of time before bulges, blisters, or outright failures evolve. In such instances, a metallurgical check-up in addition to an examination of the contributing mechanical factors can be useful in finding out the cause of the problem.
A long-term scaling condition (poor water treatment) which will lead to a tube leak is usually indicated by a wrinkled, bulged external area and an ultimate thick-lipped fissure or opening. This characteristic is indicative of long-term creep failure created by constant scale formation, resulting in overheating and swelling of the tube exterior in the form of a bulge or blister. The scale will tend to crack off; water contacts the metal and cools it until further scaling continues. The iron oxide layering on the outside surface splits during the action, giving rise to the characteristic longitudinal creep cracks.
Failures Due To Corrosion
There are a wide variety of failures that can happen due to corrosion. So much so, that we created a 6-part series to go over them! You can read the series in its entirety using the links below, and contact Complete Water Solutions today for help with your boiler water system.