Monitoring and Control of Your Water Treatment System – Part 5
Monitoring and Control of Your Water Treatment System - Part 5
Continuous On Line Monitoring
Using the Baetz Model Condenser, test simulation occurs measuring surface condenser fouling and corrosion. It is made up of a horizontal, cylindrical stainless steel she made up of one, two, or four removable tubes. The tubes then run the width of the shell, terminating at the tube sheets. The heat flux is generated by an electrical heater located at the bottom of the shell. Temperature sensors are located in the tube discharge as well as in the shell.
This test is very similar in principle as of that of a standard surface condenser. First, the test water flows through the tube, discharging to drain. Distilled water fills the shell, covering the electric heater but remaining below the tubes. Â A vacuum of 27 inches of mercury is applied to the shell to simulate condenser conditions. Heat is then applied to the distilled water by the use of the electric heater, causing the water to boil, creating a rise in vapor collecting in the tubes. The steam is condensed on the tube surface, by sending cool water through the tubes. The condensation then falls to the reservoir of distilled water and the cycle repeats itself.
The model condenser simulates operating conditions, such as heat flux and tube side velocity. The tube discharge temperature and shell temperature are monitored continuously. As foulant accumulates on the internal tube surfaces, less heat is transferred through the tube wall. As a result, the tube discharge temperature decreases while the shell temperature increases. At a constant flow rate, the increase in the temperature difference can mirrors a fouling factor by the same equation given for the MonitAll. Typically, further analysis is performed on the removed tubes that are sent to a laboratory.
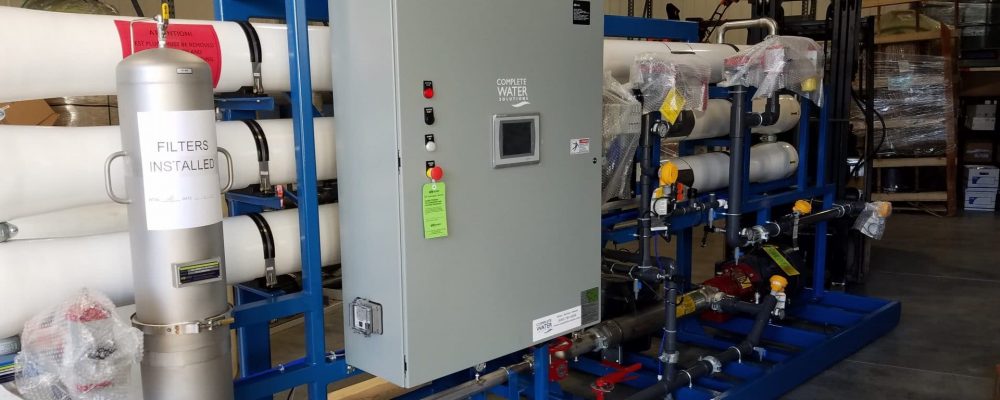
Test Heat Exchanger
A test heat exchanger is used to monitor the fouling and corrosion tendencies of a particular cooling water stream. Cooling water passes through the two removable tubes that are contained in a cylindrical shell. The tubes are available in many different materials and can be designed to accommodate a two single-pass or one two-pass operation. The steam then flows into the shell and heats the water flowing through the tubes. The steam then exits the shell through a flowmeter that is used to monitor the input of the heat.
The Cooling System Monitoring Station also is known as COSMOS™ . When monitoring and analyzing the key operating parameters, this is an important tool in the development of an effective cooling water treatment program. The Betz Cooling System Monitoring Station (COSMOS ) is an exact tool that is designed to be used for this purpose. It monitors conductivity, corrosion and pH rates. In addition, a MonitAll® hot tester can be included for the evaluation of fouling factors, water velocity, and heat flux. A wide variety of metals and materials can be evaluated.
The monitoring station consists of two separate units: an instrumentation and piping cabinet and a data acquisition cabinet shows the data acquisition cabinet, with the panel door open, connected to the piping and instrumentation cabinet.
The wet side of the piping and instrumentation cabinet and includes the MonitAll hot tester, two corrosion probes a flow sensor, a pH sensor, a conductivity sensor, stainless steel piping, coupon holders, and a drain line. The electrical power for the MonitAll and the space heater provided for climate control are housed in a small electrical enclosure within the cabinet.
The data acquisition cabinet contains the microprocessor-based controller, which manages all of the display, data acquisition, and storage. The cabinet also controls a printer, the floppy disk drive, automatic corrosion probe switching, automatic shutdown safeguards and alarms, and all of the climate controls. The device operator has a controller with a keypad and a display window for an easy user interface. A small server or personal computer can be used to generate graphs, reports, and statistics to be analyzed from the data.