Introduction to Filtration for Parts Washers
Introduction to Filtration for Parts Washers
Parts, when manufactured and before assembly into finished products, often require cleaning to reduce manufacturing debris to meet product quality specifications. This results in the ability to use these components in equipment with increasingly tighter manufacturing tolerances. In the past, solvent systems were quite common, but the EPA has instituted guidelines restricting solvent usage in the parts cleaning marketplaces. The search for alternatives to solvent cleaning technologies resulted in new solutions for high technology critical cleaning applications. Today, parts cleaning applications continue to increase, with most of the applications being water-based detergent processes.
Manufacturers in all industries want to know how the cleaning process can be improved… made faster, more effective, and less expensive. To achieve the required improvements and effectively increase both efficiencies and yields, parts washing systems must:
• Maintain clean wash and rinse tank fluids through appropriate filtration,
• Provide the degree of cleanliness required to reduce scrap or cleaning rework, while decreasing system maintenance.
Selection of the correct filters for these applications has proven to reduce the overall manufacturing costs…rework, scrap, customer rejects and help to extend the life of washing and rinsing fluids. Inadequate or no filtration at all will increase the number of off-specification parts produced while maintaining a cleanliness level exceeding the required specification will consume resources unnecessarily.
The Industrial Parts Washing Process
Most, if not all, parts washing equipment is custom designed for the intended application. This includes peripheral equipment such as a filtration system. The level of filtration or cleanliness requirement of the part is dictated by where and how the part will be used. Parts being cleaned are typically transported to the cleaning system by an overhead conveyor or placed on a conveyer belt. Small parts or components are either: 1.) placed in an enclosed basket and immersed into a bath, 2.) or nested, in a tray or fixture, and sprayed. The cleaning process consists of a series of stations each having dedicated tanks for washing and rinsing. The first stations in the cleaning process, Figure 1, are dedicated to washing. The parts, if immersed, may undergo a very rigorous cleaning cycle. Often an immersed basket of small parts will be lowered and raised in the bath several times, tumbled, undergo ultrasonic cleaning, or a combination of the above methods. Exiting the first wash station, the parts will pass to the second wash station. The process is similar to the first but conducted in a “cleaner tank”. The parts will eventually leave the wash area and enter the first of two or more rinse stations. The rinse process is generally limited to a spray rinse or to immersion and tumbling of the parts. The final rinse is the cleanest water the parts will encounter and this will determine the cleanliness of the part. Each wash and rinse tank has a dedicated filtration system for the reduction of contaminants. The water is pumped from the tank, through a filter, and returned to the tank. Common contaminants carried into the system along with the part being cleaned are oils, emulsified oils and solid particulate.
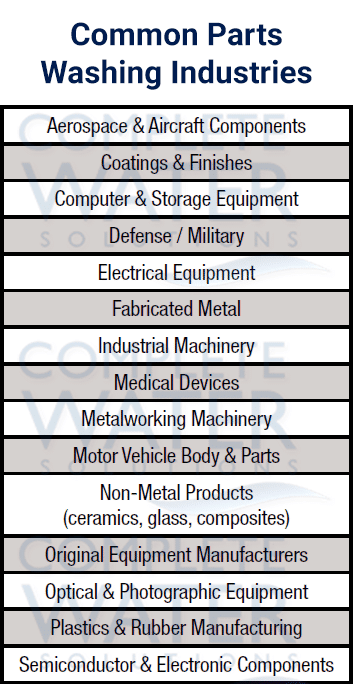
Potential Parts Cleaning Problems
The parts cleaning operation is effectively a closed loop system where the goal is to regenerate constantly and reuse the wash and rinse tank fluids. This is often the most cost effective process to use, avoiding constant bath change and chemical addition. The problem in maintaining such a system is that particulate, oils and surfactants are constantly being introduced into the wash and rinse fluids as the parts being cleaned are moved from tank to tank being sprayed or dipped. These contaminants and manufacturing debris, if not effectively reduced, will build up over time, changing the chemistry of the parts cleaning solutions, and inhibit the solution’s ability to clean the parts effectively and, therefore, meet cleanliness specifications. These contaminants also have a significant impact on the fluid treating equipment – used to maintain appropriate hardness, pH, and other critical water chemistry requirements – as follows:
Wash/Rinse Tanks
If the fluid in the wash and rinse tanks do not maintain the specified cleanliness levels, often measured in mg/l or ppm, the parts, as they are passed from tank to tank, will not be adequately cleaned of particles and debris. The result is:
• parts will not meet specification, will be rejected and have to be cleaned again. This results in reduced productivity and increased inventory levels.
• defective (poorly cleaned) parts are shipped to customers, or used in equipment. The resulting machine debris may cause unnecessary wear to the finished products, reducing equipment life or simply creating poorly performing equipment and potential rework on a warranty.
To maintain the bath cleanliness specifications, parts cleaners will often change the bath fluids, causing disposal and waste problems. The cost of disposal, including labor and washing fluid replacement, combined with the lost production can have a significant impact on the parts cleaning operations profitability.
Ultrafiltration (UF system)
The purpose of the UF system is to reduce emulsified oils that are introduced into the wash bath by the parts undergoing the washing. The UF system works on the principle of passing a stream of contaminated water over a micro porous membrane which often has pore sizes smaller than 0.1 micron in order to separate the unwanted contaminants from the feed stream. As the fluid passes over the membrane, two streams are ejected. Purified water, virtually free of oils and particles, preferentially permeates through the membrane and returns to the wash tank to be reused. Emulsified oils and particles can not permeate through the membrane and are ejected in the concentrate stream. UF membranes are very expensive, typically costing thousands of dollars each, and are expected to be in service for years. If not properly protected, the membrane will plug with solid particles resulting in reduced fluid output, higher operating pressure drops, and higher energy costs. Eventually, the membrane will become completely plugged and require replacement.
Reverse Osmosis System (RO System)
RO systems reduce dissolved salts and minerals from the incoming rinse water, which, in turn, provides a spot free finish on the washed parts. Like the UF system, this is accomplished by passing the water over a micro porous membrane where the water molecules will preferentially pass through the membrane while the dissolved ionic contaminants will not. Particles in the feed water must be reduced from the water or the membrane will plug prematurely resulting in unnecessary change-out and expense.
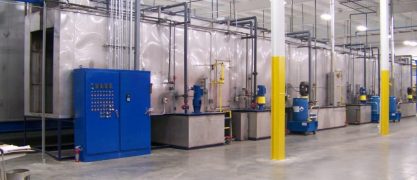
Potential Parts Cleaning Solutions
Filtration for a parts cleaning system can range from simple to complex depending on the cleanliness requirement. In complex systems, where requirements dictate finer reduction efficiencies, relatively coarse reduction of large particles occurs at the wash tanks, while finer reduction efficiencies are required at the final rinse tanks. This, along with providing sufficient protection for the ancillary water treatment systems, means that filters with different micron ratings and potentially materials of construction must be used. The filters of choice will be those that:
• are chemically compatible with the various additives and detergents added to the wash and rinse fluids to meet specifications
• have high dirt holding capacity to provide long on-stream life and reduced filter change-out for reduced disposal and maintenance costs
• are absolute-rated for the rinse stages to reduce all particles larger than the stated rating, therefore, providing reproducible and defined system protection
Since no one filter is ideal for all applications it is very important to review the requirements to obtain a cost-effective system. The listing below is a guideline to aid when reviewing the filtration requirements of the system.
1.) The initial wash stages have a significant amount of manufacturing debris that must be reduced from the wash water. Likewise, when reducing the filter from the housing, it is ideal to reduce the debris with the filter. This reduces the need to clean the filter housing during filter change-out.
2.) The secondary wash and initial rinse stations are designed to provide an improvement in the level of filtration. Absolute rated filters are ideal for this application. This assures that the desired particles are reduced form the wash and rinse water.
3.) Chemical compatibility and temperature may also limit the filter selection and it is important that the wash and rinse quality is not compromised by these constraints.
4.) The final rinse station will dictate the part cleanliness and the part can only be as clean as the rinse solution. It is therefore imperative that the filter provides the utmost quality while still being cost-effective.