Boiler Water Quality Control
Quality Control for Boiler Water
Feed Water Considerations
Boilers require external pretreatment of the feed or make-up water regardless of the type of boiler or operating pressure. Internal chemical treatment is required, regardless of the extent of the external water treatment. The external treatment reduces the chemical feed dosages and total operating costs. This publication addresses primarily the use of hardness removal equipment. Control of Total Dissolved Solids and alkalinity levels are also important and we intend to review these areas as well.
Total Dissolved Solids (TDS) Control
When water is evaporated and forms steam, the minerals or solids that were dissolved or suspended in the water remain behind in the boiler. To replace the water which is evaporated, we add make-up water with its normal load of minerals or solids. After a period of time the Total Dissolved Solids (TDS) within the boiler will reach a critical level. This level, on lower pressure boilers, is recommended not to exceed 3500 ppm. TDS above this range can cause foaming which will result in a carrying of the high concentration of TDS into the steam lines, valves, and steam traps. The increasing level of the TDS is known as “cycles of concentration.” This term is used very often in the operation and control of a boiler system. A water supply that contains 175 ppm of TDS in the make-up water could be concentrated 20 times to 3500 ppm.
The maximum amount of TDS allowed in a low-pressure boiler is 3500 ppm. On higher pressure operated boilers the TDS limit is reduced in relationship to the pressure rating. (See the table below.)
To control the maximum allowable level of TDS, the operator must open periodically the boiler’s blowdown valve. Blowdown is the first step in boiler water control and it can be accomplished manually at given intervals. The frequency is dependent on the amount of solids in the makeup water and the amount of make-up water added. In larger or more critical boilers the blowdown may be automatic or continuous.
Hardness Control
Alkalinity Control
In addition to controlling the cycles of concentration of TDS, the alkalinity must also meet the maximum criteria. The level of alkalinity within low-pressure boilers should not exceed 700 ppm. The presence of alkalinity above the 700 ppm level can result in a breakdown of the bicarbonate producing carbonate and liberate free carbon dioxide with the steam. The presence of carbon dioxide in the steam usually results in high corrosion of steam and return lines.
Dealkalization is a process whereby softened water is passed through a unit which contains anion resin. The anion resin removes anions such as sulfate, nitrate, carbonate, and bicarbonate. These anions are replaced by chloride. Salt (sodium chloride) is therefore used to regenerate the unit with the anion exchange resin.
The need to soften the water to a dealkalizer stems from the danger of hard water precipitating calcium carbonate, and magnesium hydroxide within the dealkalizer bed. In addition, the anion exchange bed is also subjected to fouling with suspended matter. Because the dealkalizer’s resin is lighter than a conventional softener resin, the backwash rate is much slower and insufficient to remove the suspended matter. The use of a softener as pretreatment serves, therefore, as an additional safeguard in the use of a dealkalizer.
As in the control of TDS there are decreasing levels of allowable alkalinity concentration as the boiler pressure rating increases. (See table below.)
The formation of scale deposits on boiler heating surfaces is the most serious problem encountered in steam generation.
The primary cause of scale formation is the fact that the solubilities of the scale-forming salts decrease with increase in temperature. Consequently, the higher the temperature (and pressure) of a boiler operation, the more insoluble the incrusting salts become.
The presence of scale within the boiler is equivalent to spreading a thin film of insulation across the path of heat travel from the furnace gases to the boiler water. The presence of the heat insulating material will retard heat transfer and cause a loss in boiler efficiency.
Even more important than the effect of scale in causing heat loss is the effect of scale in causing overheating of boiler metal and consequent tube failures. Costly repairs and boiler outage are the result of such a condition. The modern boilers with high rates of heat transfer, the presence of even extremely thin deposits of scale will cause serious elevation in the temperature of tube metal. The scale coating retards the flow of heat from the furnace into the boiler water. This heat resistance results in a rapid rise in metal temperature to the point at which failure results. The possible damage of such a failure is not only expensive, it is also dangerous, since the metal is under pressure.
The real fact on the data provided here is that the presence of any scale should be prevented from forming in boilers by either internal (chemical) or external (water softener) methods.
Most scale can be prevented from forming in boilers by the employment of external (water softener) treatment. However, no system of external softening, regardless of the high degree of efficiency, is in itself adequate protection against boiler scale. The use of internal (chemical) treatment is also required as supplementary to an effective boiler scale control program. However, there will remain some small amount of hardness in the feedwater even with the use of a water softener. Therefore, chemical treatment is always required. Internal treatment alone is more expensive and increasingly so at higher hardness levels. The employment of a water softener in conjunction with a chemical treatment program is the most effective, reliable, safest, and economical means of boiler water quality control.
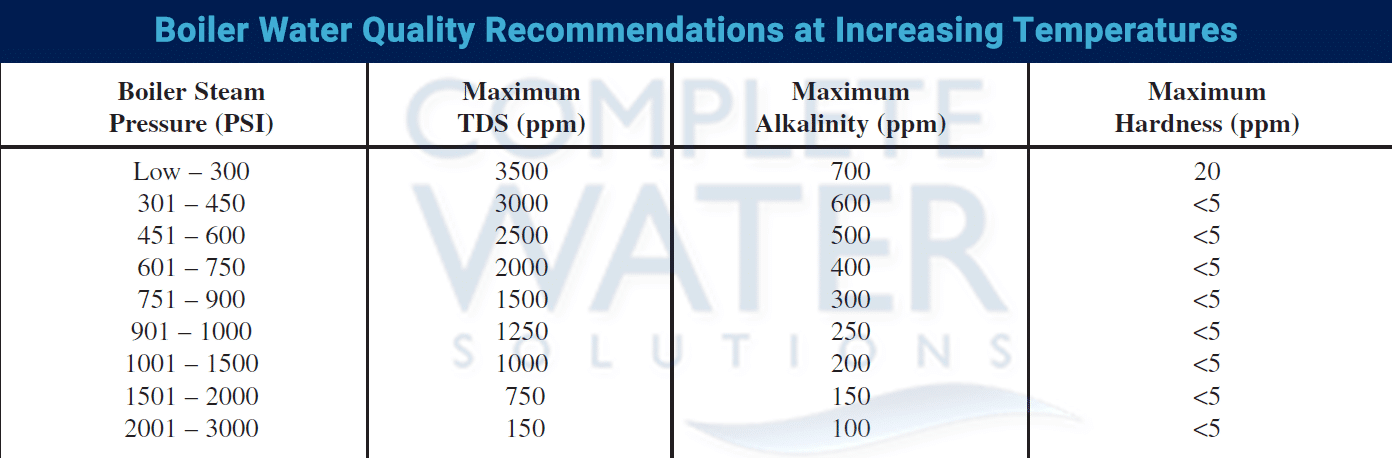
These are common recommendations! – Every boiler manufacture has recommended operating parameters for water quality.
We @ CWS recommend consulting with the boiler manufacture to verify water quality parameters. Then contact complete water solutions to determine what you need to get there!
Quality Water Summary
Total Dissolved Solids (TDS)
The maximum allowable concentration of TDS within a low pressure boiler is 3500 ppm.
Alkalinity
The maximum allowable concentration of alkalinity within a low pressure boiler is 700 ppm.
Hardness
The maximum allowable hardness within any boiler should approach 3 – 5 ppm.