Boiler Failures Due to Corrosion – Part 3
Boiler Failures Due to Corrosion – Part 3
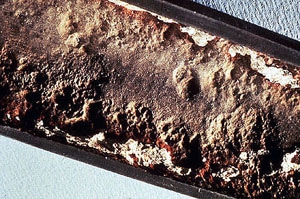
Caustic Attack
Some boiler failures due to corrosion may be the result of a caustic attack. Caustic attack (or caustic corrosion) is encountered in boilers with demineralized water and most often occurs in phosphate-treated boilers where tube deposits form, particularly at high heat input or poor circulation areas. Deposits of a porous nature allow boiler water to permeate the deposits, causing a continuous buildup of boiler water solids between the metal and the deposits. The thinning caused by caustic attack assumes irregular patterns and is often referred to as caustic gauging (like in the image on the left). When deposits are removed from the tube surface during examination, the characteristic gouges are very evident, along with the white salts deposit which usually outlines the edges of the original deposition area.
Steam Blanketing
A number of conditions allow stratified flow of steam and water in a given tube, which usually occurs in a low heat input zone of the boiler. This problem is influenced by the angle of the affected tubes, along with the actual load maintained on the boiler. Stratification happens when velocity is not sufficient enough to maintain turbulence or thorough mixing of water and steam during passage through the tubes. Stratification most commonly occurs in sloped tubes located away from the radiant heat zone of the boiler. Examination of the affected tubes usually reveals a prominent water line with general thinning in the top area of the tube or crown. In rare occasions, the bottom of the tube is thinned. When the boiler water contains caustic, high concentrations accumulate and lead to caustic corrosion and gouging under the deposits that accumulate at the water line.
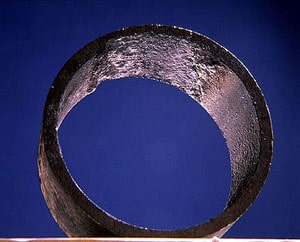
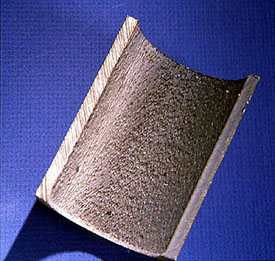
Acidic Attack
Acid attack of boiler tubes and drums is usually in the form of overall thinning of all surfaces. This results in a visually irregular surface appearance, like in the image on the left. Smooth surfaces appear at areas of flow where the attack has been intensified. In severe occurrences, other components, such as baffling, nuts and bolts, and other stressed areas, may be badly damaged or destroyed, leaving no doubt as to the source of the problem. Intense occurrences of acid attack can usually be traced to either an unsatisfactory acid cleaning operation or process contamination. Some industrial plants encounter periodic returned condensate contamination, which eliminates boiler water alkalinity. Occasionally, regeneration acid from an ion exchange process is discharged accidentally into the boiler feedwater system. Cooling water contamination of condensate can depress boiler water pH and cause severe deposition and pitting in areas of high heat flux. Damage can be quite severe if immediate steps are not taken to neutralize the acid.