Boiler Failures Due to Corrosion – Part 2
Boiler Failures Due to Corrosion – Part 2
Dissolved Oxygen
Dissolved oxygen corrosion is a constant threat to feedwater heater, economizer, and boiler tube integrity. As deposit control treatment methods have improved, the need for effectual control of oxygen has become progressively important. The use of chelant treatments and demineralized water has improved the cleanliness of boiler heat transfer surfaces to such an extent that essentially bare-metal conditions are common. Only a thin, protective, magnetic oxide film remains in such instances. Therefore, oxygen control has become even more essential today. The use of catalyzed sulfite, where applicable, is a standard recommendation in chelant applications. The control of downtime corrosion has become increasingly important in recent years to prevent or inhibit pitting failures. Often, cold water that has not been deaerated is used for rapid cooling or start-up of a boiler. This is a risky operating practice, usually chosen for economical reasons. Severe pitting can occur in such instances, especially in boilers that have been maintained in a deposit-free condition. Therefore, it is usually more economically efficient to maintain clean heat transfer surfaces and eliminate the use of cold water containing dissolved oxygen during cool-down and start-up periods. This practice can result in fuel savings and improved boiler reliability.
Chelant Corrosion
Chelant corrosion of boiler metal occurs only when surplus concentration of the sodium salt is maintained over a period of time. The attack is of a dissolving or thinning type-not pitting-and is concentrated in areas of stress within the boiler. It causes thinning of rolled tube ends, threaded members, baffle edges, and similar parts of stressed, unrelieved areas. Normally, annealed tubes and drum surfaces are not attacked. When tube thinning occurs in a chelant-treated boiler, evidence of steam blanketing and/or film boiling is sometimes present. In such instances, failure occurs regardless of the type of internal treatment used. Pitting is often thought to be a result of chelant attack. However, pitting of carbon steel boiler tubes is almost always due to the presence of uncontrolled oxygen or acid. Infrequently, copper plating (usually the result of an improper acid cleaning operation) may lead to pitting problems. Being aware of boiler failures due to corrosion from chelant allows you to be aware of potential problems sooner.
Stress-Induced Corrosion
Certain portions of the boiler can be very susceptible to corrosion as a result of stress from mechanical forces applied during the manufacturing and fabrication processes. Impairments are commonly visible in stressed components, such as rolled tube ends, threaded bolts, and cyclone separators. However, corrosion can also occur at weld attachments throughout the boiler (see image) and can remain undetected until failure occurs. Regular inspection for evidence of corrosion is recommended because of the potential for an explosion caused by a tube leak. The potential for stress-induced corrosion can be reduced if the following factors are minimized: stresses developed in the boiler components, the number of thermal cycles, and the number of boiler chemical cleanings. In addition, it is necessary to maintain proper water chemistry control during operation and to provide protection of boiler failures due to corrosion during shutdowns.
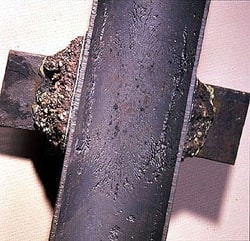