7 Common Causes of Membrane Fouling & Degradation
What Are Common Causes of Membrane Fouling & Degradation?
Feed Water Considerations
Fouling is a process during which continuous buildup of contributing deposits reduce the function and efficiency of the operating system. Membrane systems are mechanical and therefore subject to fouling on the surface. This fouling ultimately degrades the membranes. There are 3 main causes of degradation – oxidation, hydrolysis due to pH extremes, and exceeding the maximum operating temperature – and 4 main causes of fouling – suspended solids, organic, scaling, and biological – that effect RO and NF membrane performance.
Oxidation
Chlorine, chloramines, ozone, hydrogen peroxide, and other chemicals are oxidizers and will attack the structure of the membrane’s concentrate layer. This does damage some layers, such as the thin film composite layer, more than others. There are precautions you can take, such as maintaining chlorine concentrations at less than 0.01 ppm. Metals such as iron and copper, when in the feed water, increase the rate of oxidation. If the damage from oxidation is extensive then salt rejection will drop. Once it drops to a certain point, running the equipment and ionic loading on downstream ion exchange equipment will exceed the cost of replacing damaged membranes.
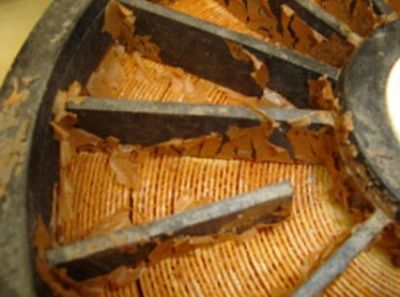
pH Extremes
Hydrolysis is a chemical change that decomposes the membrane and can be caused by extremes in pH balance. A membrane’s thin film composite layer will operate at a pH level of 2-11. The cellulose acetate membrane’s pH range is 5-8. Beyond this range, one both accounts, hydrolysis occurs. This damages the membrane polymeric structure and the glue joints on membrane leaves and the feed channel spacer. The membrane, under these conditions, will perform poorly.
Temperature
When temperature limits are exceeded, thermal damage occurs for the membrane, leaving it generally useless. The maximum temperature limit for cellulose acetate membranes is 35 degrees Celsius, and for most thin film composites, the temperature maximum is 45 degrees Celsius. After the temperature exceeds this, the membrane is a total loss.
Suspended Solids
Suspended solids in the feedwater deposit on the membrane surface. This blocks feed channels and can especially cause problems for a system’s lead membranes. Some suspended solids that may cause this are silt, clay, silica, iron, manganese, and aluminum. Disperants and surfactants can be used to clean fouled membranes.
Scaling
Substances such as calcium, barium, strontium silica, and other salts can become super saturated at the surface of a membrane, reducing the amount of water that can pass through the feed channel and permeate through the membrane. Applying low pH acidic solution to the membrane is a common cleaning process for this. If silica fouling occurs, which is not as common, it will be much more difficult to clean and will require a different, more specialized technique.
Organic
Naturally occurring organics found in surface water can be a cause of membrane fouling. Other examples besides organic fouling are coagulants (or flocking agents) and incompatible pretreatment chemicals. Typically, the cleaning process for organics is by applying high pH solution. Occasionally, a more specialized method of cleaning may be necessary, but this depends on the foulants present.
Biological
Biological material may grow on the surface of the membrane, reducing the feed channel and permeate flows. Fouling component examples are organic slimes and bacteria. A high pH cleaner combined with disperants at high temperatures and applied at turbulent rates of flow will remove biological material. Overnight soaking may be necessary if high biofouling is present.