Getting to Know Chemical Feed Systems – Part 3
Getting to Know Chemical Feed Systems - Part 3
More Chemical Delivery Systems
As previously stated, delivery systems are the central key to a chemical feed system. Although most commonly used delivery systems are through the metering pump, there are several more options. In “Getting to Know Chemical Feed Systems – Part 2” you learned about metering pumps, packed plunger pump, and diaphragm pumps. On this page you will learn about rotary pumps, gravity feed, water-jet eductor, and accessories.
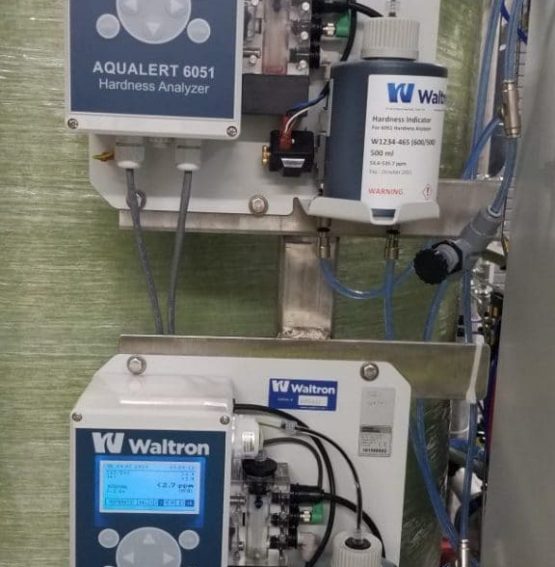
Gravity Feed
Gravity feed design is another commonly used delivery system. This system uses the height different between chemical in the tank and the point of application as the driving force. A dominant advantage to using a gravity feed delivery system is because of the reliability and directness. It is pumpless, which removes changing parts and required maintenance that goes along with those parts. The elimination of check valves and their failures from time to time directly impacts reliability. Gravity feed can offer precise chemical control when feed verification methods are engaged.
There are multiple types of gravity feed designs. One example is the shot feeder. It is simple, yet very effective in dispensing premeasured chemical “shots”. With this type of system a measuring pot of a designated volume is filled from the bulk storage tank. Which then a valve at the bottom of the measuring pot is opened and the product is allowed to move by gravity into the system.
You can reach feed verification by measuring the velocity of product movement or volume per time. This will give you accurate measurement and feed of product to a system without the typical maintenance issues that go along with metering pumps. The most advanced gravity feed systems will combine feed verification with computerized controls allowing for optimal chemical control and reduce the necessity of a metering pump.
Having the appropriate size system is necessary. If your system is too large, it can cause a jump in chemical treatment, or even overfeeding. If your system is too small, you could possibly not feed enough chemicals into your treatment. These variables must be looked at when purchasing this type of chemical feed system. Looking at viscosity, the effect of fluctuating tank levels can allow static head, and system friction losses will aid in determining the correct gravity feed system.
Rotary Pumps
Rotary pumps can have one to two rotating parts to give positive or semi-positive displacement. The pump may have a single rotating member or two meshing gears in an eccentric housing. With a full positive displacement type, the delivery rate is set by the speed of rotation. Semi-positive displacement pumps have slippage internally, which affects discharge pressure and delivery rate. Rotary pumps typically count on the fluid being pumped for lubrication. Many designs do not allow abrasive material in the fluid. However, rotary pumps can pump highly viscous fluids and are beneficial for polymer applications. Having a low shear will help it pump more efficiently.
Water-Jet Eductor
A water-jet eductor utilizes the kinetic energy of a moving liquid under pressure. It will catch on another gas, gas-solid mixture or liquid, mix it with the liquid under pressure, and in turn release the mixture against counter-pressure. Using this type of system can limit the amount of suction or lift needed, the accessible motive pressure, and the release pressure.
When operated in partnership with a valve, a water-jet eductor can be used for a continuous dose of chemicals into a water stream. The water-jet educator is essential for vacuum-type chlorinators and sulfonators and is used for transporting dry polyelectrolytes. It is typically used for mixing applications instead of proportioning.
There are several perks to using a water-jet eductor, such as low cost, ability to self-prime, and no moving components. With these delivery systems not needing electrical power to operate, they work well for unsafe areas where expensive explosion-proof equipment is needed. They can be adapted to work with automatic control systems as well.
Having filters and strainers can help in reducing accumulation of particulate matter around and in the eductor nozzle, which can lead to a loss of suction. Water-jet eductors need to be inspected and cleaned on occasion in locations that deposition may occur.
Accessories
Pump/Tank Packages: In many applications, having only a pump will not suffice for chemical feed. Typically, a chemical feed system incorporates a pump, tank, valve, mixer, gauges, strainer and relief valves, mixing, and pumping. Items included in the package depends on if mixing is required and if chemical solution preparation is needed.
Mixers: The most common form of mixer used for chemical feed systems is a vertically attached, shaft-driven impeller. If the chemical is a diluted, high molecular weight polymer, a speed reducer might be necessary. Some chemicals require minimization of air entrainment. In that situation, an air-driven recirculation pump or an electrical pump should be applied for mixing.
Timers: Timers are used for several applications in chemical feed systems. Most often they are used for the control of mixers and batch feeding of chemicals, typically antimicrobials.
Alarms: Alarm systems are increasingly becoming more advanced. You are now able to monitor and alarm based on chemical use rates, pump status, low and high tank levels, and any unusual operating conditions.
Injection Nozzles: Particular nozzles, low and high-pressure, are needed to inject chemicals into pipelines. Low-pressure nozzles are utilized for injecting into a liquid stream. High-pressure quill nozzles are used with vapor systems. The quill allows the chemical to be expelled into fine droplets that are carried with the vapor steam. Efforts should be made to prevent injection of liquid into steam lines immediately upstream of pipe bends, where high-velocity liquid droplets can influence and erode pipe walls.
Level Gauges: The demand for monitoring on-site and remote tank levels has driven the development of several different sorts of monitors. Some of the leading methods are pressure transducers, ultrasonic monitors, pressure-sensitive potentiometers, capacitance sensors, and bubble tubes. Efforts should be made to ensure the compatibility with the materials of construction, adequate temperature compensation, and isolation from damaging pressure shocks.