Boiler Failures Due to Corrosion – Part 1
Boiler Failures Due to Corrosion - Part 1
Stress Corrosion Cracking
There are various corrosion mechanisms that contribute to boiler tube failures. Stress corrosions can result in either intercrystalline or transgranular cracking of carbon steel. This is caused by a combination of metal stress and the presence of a corrosive. To determine the extent and specific type of cracking that has occurred, a metallurgical examination of the specific area is necessary. When the type of cracking is specified, proper corrective action can be taken.
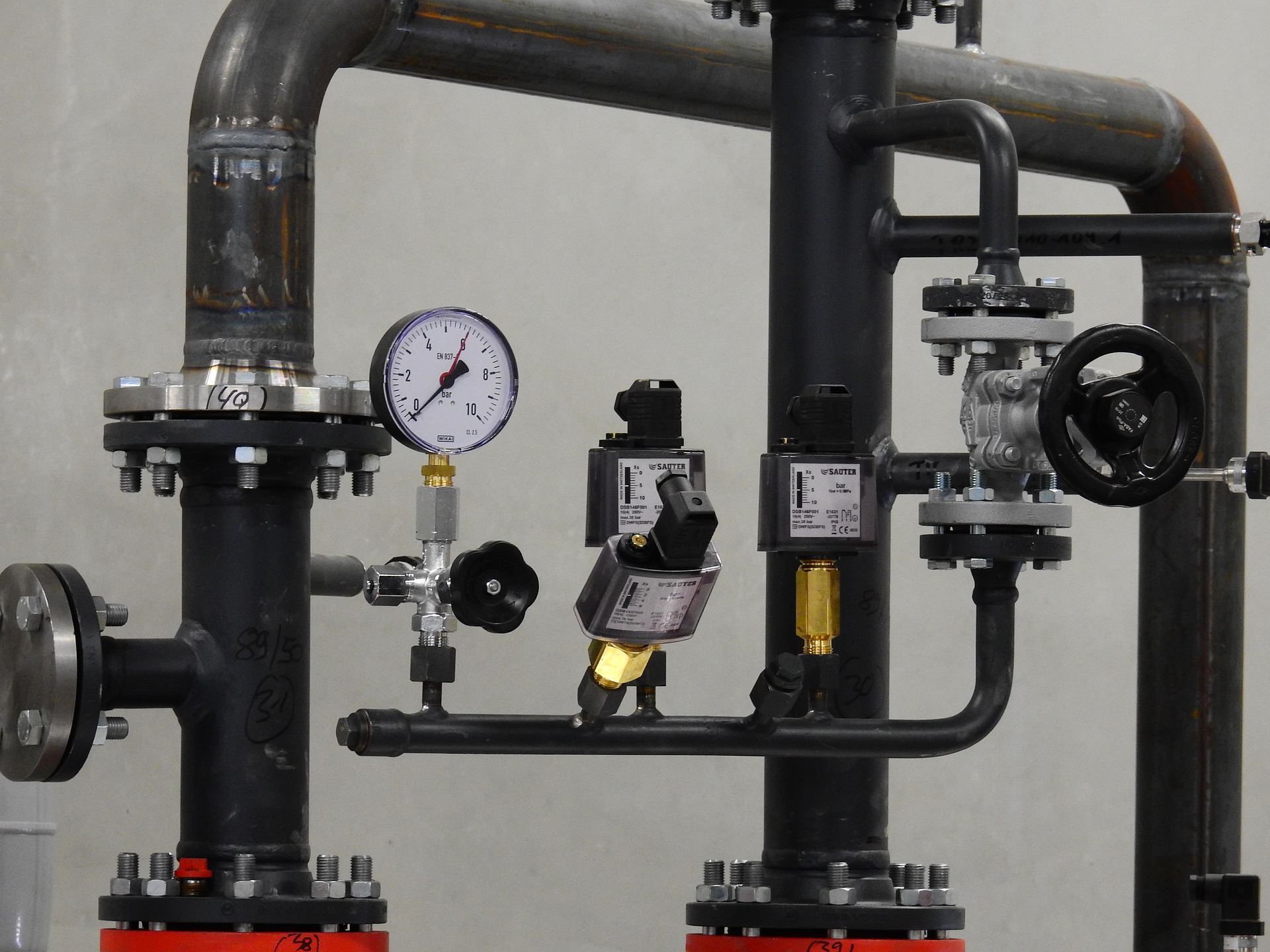
Fatigue and Corrosion Fatigue
The most common form of cracking found in industrial boilers is transgranular cracking which occurs primarily due to cyclic stress. To find the cause of transgranular failures, both the design and the operating conditions of the boiler must be analyzed. Straight tube, shell-and-tube waste heat boilers frequently develop tube and tube sheet failures due to the demands of the unequal stresses. This is primarily caused by the uneven distribution of hot gases across the face of the tube sheet. Leaking problems are created when the tubes come loose. Imposed stresses can cause transverse cracking of the tubes, even if they are securely welded.
In mechanisms that are designed to allow steam pockets to form within a unit cyclic overheating quenching can also occur, leading to transverse cracking of tubes and, occasionally, shells. This type of cracking arises in the area of greatest stress and results in primarily transgranular cracks.
Some intercrystalline cracking may develop in this type of failure whether or not free NaOH is present. The most common type of cracking is still across the grain structure of the metal. Due to it being mechanically induced, the cracking happens despite boiler water chemical concentrations. There can also be a number of pits adjacent to or in line with the cracking – another specific indicator of apparent mechanical stresses. Any corrosives present to contribute to the formation of these pits. The normal reaction between iron and water is sufficient to cause pitting at breaks in the thin oxide film formed on freshly exposed surfaces under stress.
Caustic Embrittlement
A specific form of stress corrosion is caustic embrittlement, which develops into the intercrystalline cracking of the steel mechanism. This type of cracking only results when all of the following are in existence in the appliance: specific conditions of stress, a mechanism for concentration such as leakage, and free NaOH in the boiler water.
Even if the boiler is of an all-welded design, there is still a possibility that embrittlement can occur. Cracked welds or tube-end leakage can provide the mechanism by which drum metal may be negatively affected. When free caustic is present, embrittlement is possible.
An embrittlement detector may be used to determine whether or not boiler water has embrittling tendencies. If there are embrittling characteristics present in the boiler water, a course of action must be initiated to prevent the boiler from experiencing an embrittlement-related failure.
Sodium nitrate is the regular treatment for repressing embrittlement in boilers operating at low pressures. The ratios of sodium nitrate to sodium hydroxide in the boiler water recommended by the Bureau of Mines depend on the boiler operating pressure.
Pressure, PSI | NaNo₃/NaOH Ratio |
---|---|
Up to 250 | 0.20 |
Up to 400 | 0.25 |
Up to 1000 | 0.40-0.50 |
The formula for calculating the sodium nitrate/sodium hydroxide ratio in the boiler water is:
NaNO₃ | ppm nitrate (as NO₃-) | |
__________ | = | _______________________ |
NaOH | ppm M alkalinity – ppm phosphate (as CaCo₃)(as PO₄³-) |
At pressures above 900 psig, coordinated phosphate/pH control is the usual internal treatment. This particular treatment method deters any development of high concentrations of caustic, thus eradicating the potential for caustic embrittlement.