Boiler Failures Due to Corrosion – Part 6
Boiler Failures Due to Corrosion - Part 6
Procedures for Boiler Tube Failure Analysis
When the cause of boiler failure is not immediately apparent, it can be difficult to determine the next steps for corrective actions. A comprehensive investigation of the failure and associated operating data is usually helpful in distinguishing the specific cause of failure so that corrective action may be taken.
To obtain accurate metallurgical analyses of the boiler tubes, proper investigative procedures are required. In some situations, a macroscopic examination coupled with chemical analysis and microscopic analysis of the metal may be needed to evaluate the primary failure mechanism(s). When the failed tube section is removed, precautions must be taken to avoid the contamination of deposits and damage to the failed areas. All removed pieces should be accurately labeled with their location and orientation.
Normally, a chemical analysis of a deposit from a certain area is wanted. Scanning electron microscope-energy dispersive spectroscopy (SEM-EDS) is a multifaceted technique that enables inorganic chemical analysis on a microscopic scale.
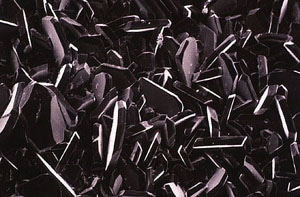
These SEM-EDS can also be useful in determining the following:
- Discrepancies in deposit composition between corroded and uncorroded areas on a tube surface.
- The extent to which the under-deposit collection of boiler salts on heat transfer surfaces is promoting corrosion damage.
- Elemental variations between visually different tube surface deposits.
Inorganic analyses through SEM-EDS can also be implemented on ground and polished cross-sections of a tube covered with thick layers of waterside deposit. This is called elemental mapping and is helpful when the deposits are multilayered. Cross-sectional analysis of boiler deposits can also identify periods when there have been upsets in water chemistry, which then provides data to help determine the time and reasons for the deposits formed. Represented by color-coded dot maps, the spatial distribution of elements in a deposit cross-section is shown in elemental mapping. Separate elements of interest can be expressed by individual maps, or selected combinations of elements can be designated on composite maps.
A scanning electron microscope (SEM) can analyze the topography of surface deposits and/or morphology of fracture surfaces. Fractography can classify a failure mode. For example, microscopic features of a fracture surface can determine whether the steel failed in a brittle or ductile manner, whether cracks propagated through grains or along grain boundaries, and if fatigue (cyclic stress) was the primary cause of failure. SEM-EDS testing can be used to distinguish if a specific ion or compound played a role in a failure mechanism through a combination of fracture surface analysis and chemical analysis.
Analysis Procedures
The first step in the investigation is a meticulous visual examination. Both the fireside and the waterside surfaces should be inspected for failure or evidence of impending failure. Photographic documentation of the as-received condition of tubing is helpful and can be used in the correlation and interpretation of data found throughout the examination. Color and texture of deposits, fracture surface location and morphology, and metal surface contour should all be given special attention. A stereo microscope allows detailed examination under low-power magnification.
It is important to analyze the dimensional attributes of a failed tube. Calipers and point micrometers are helpful tools that allow quantitative assessment of failure characteristics such as bulging, wall thinning at a rupture lip, and corrosion damage. The amount of ductile expansion and/or oxide formation can help indicate the primary failure mechanism. External wall thinning from fireside erosion or corrosion mechanisms can result in tube ruptures which often imitates the characteristics of overheating damage. In those cases, dimensional analysis of nearby areas can help to determine whether or not significant external wall thinning occurred prior to failure. Photographs of a nearby tube cross section taken of a failure site can aid in dimensional analysis and give definite documentation.
A tube surface’s cracking extent, orientation, and frequency can be used to isolate a failure mechanism. While overheating damage usually causes longitudinal cracks, fatigue damage commonly results in cracks that run transverse to the tube axis. In particular, zones adjacent to welded supports should be checked closely for cracks. It may be necessary to emplow nondestructive testing (e.g., magnetic particle or dye penetrant inspection) to identify and assess the extent of cracking.
While most water-bearing tubes used in boiler construction are fabricated from low-carbon steel, steam-bearing (superheater and reheater) tubes are commonly fabricated from low-alloy steel that includes differing levels of chromium and molybdenum. Chromium and molybdenum increase the oxidation and creep resistance of the steel. It is important to have a portion of the tube analyzed for alloy chemistry to obtain an exact evaluation of metal overheating. Alloy analysis can also identify if the tubing is within specifications. Though it is not common, the initial installation of the wrong alloy type or tube repairs using the wrong grade of steel can occur. In these cases, chemical analysis of the steel is used to define the cause of premature failure.
It may be necessary to estimate the mechanical properties of boiler components, in some cases. Most often, this involves measuring the hardness, which can be used to estimate the tensile strength of the steel. This is particularly useful in documenting the deterioration of mechanical properties that occurs during metal overheating. Usually, a Rockwell hardness tester is used; however, it is sometimes advantageous to use a microhardness tester. For example, microhardness measurements can be used to obtain a hardness profile across a welded zone to assess the potential for brittle cracking in the heat-affected zone of a weld.
Microstructural analysis of a metal component is especially important in administering a failure analysis investigation. This testing, called metallography, is useful in determining the following:
- Whether a tube failed from short-term or long-term overheating damage.
- Whether cracks opened on a waterside or fireside surface.
- Whether cracks were created by creep damage, corrosion fatigue, or stress-corrosion cracking (SCC).
- Whether tube failure occurred from hydrogen damage or internal corrosion gouging.
It is important to have proper sample orientation and preparation in microstructural analyses. The orientation of the sectioning is determined by the specific failure characteristics of the case. Carefully selected metal specimens cut with a power hacksaw or an abrasive cut-off wheel can then be fixed in a resin or plastic mold. After positioning, the samples are ground and polished to obtain a flat, scratch-free surface of the metal in the zone of interest. Once processed, a proper etchant is applied to the polished metal surface to reveal microstructural constituents (grain boundaries, distribution, and morphology of iron carbides, etc.)
Metallographic analysis of the mounted, polished, and etched sections of metal is performed with a reflective optical microscope. This is accompanied by a comparison of microstructures perceived in various areas of a tube section-for example, the heated side versus the unheated side of a water wall tube. As the microstructure on the unheated side often reflects the as-manufactured condition of the steel, comparison with the microstructure in a failed region can show the degree and extent of localized deterioration.
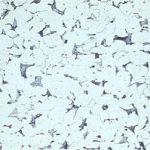
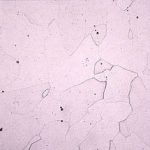
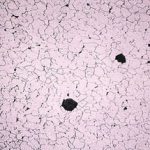
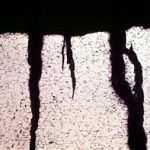