Carbon tower media can be used to remove many things in water. Some applications include removing chlorine upstream from reverse osmosis equipment or removing any impurities that may cause issues with the quality of a product that uses the water as an ingredient. An example of using water for a product would be Beverage Manufacturing. In beverage manufacturing, carbon media can help with items such as color and odor, allowing for a more consistent product.
Carbon media can come in various sizes and some material options. The most common carbon used is coconut shell and coal-based materials.
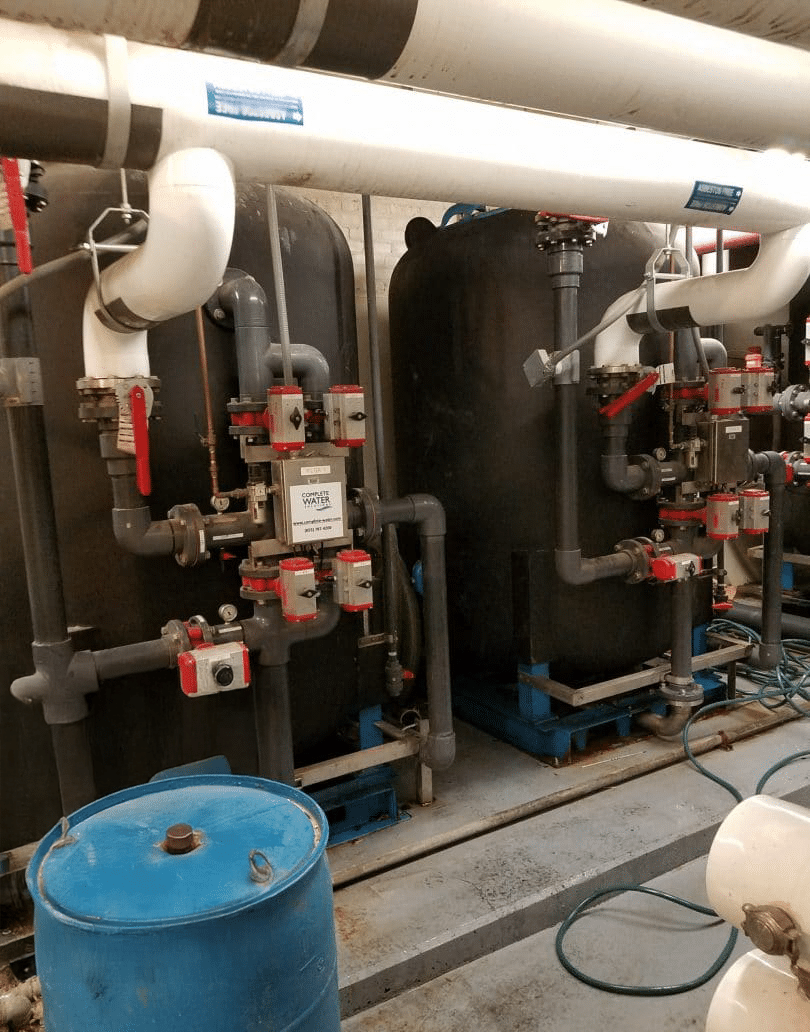
When To Change Your Carbon Media Or Carbon Tower?
This question can sometimes be complicated to answer, as water sources and quality can vary causing the carbon media to have a shorter or longer life. Carbon media can be tested to get a general idea of media life. One common test is an iodine test. When looking at a data sheet of carbon, you may find a section that provides an iodine number. This iodine number is in reference to the potential color removal from an iodine solution. The same test can be performed on carbon media that has been in service to give you a general idea of the effectiveness of the current carbon bed.
Application or validation may also dictate when the media needs to be changed out. For example, in beverage production, carbon may need to be changed on a routine schedule or validated schedule of every three years.
How To Change Out Carbon Media?
Depending on the size of the system and set up can lead to the answer of “how to change carbon media”. Before disposing of carbon media, always check with your waste removal company as they may require a test to be performed prior to disposing of.
Fiberglass media tanks: Some smaller fiber glass and poly tanks may allow extraction that can be used to slurry the carbon media out of the tanks into a waste container that will allow you to dispose of the media.
Larger steel tanks: Larger steel tanks may have access to a manway or large enough access to use a pump to slurry the carbon or even a vacuum truck to remove carbon.
Large stainless steel tanks: Common in the food and beverage industry are large stainless steel vessels that have the ability to slurry the carbon media out of the tank (typically the bottom of the tank) and then slurry it back in the tank through the top. This is one of the cleanest and potentially easiest ways to complete a carbon exchange. If you’re looking to install or replace a carbon tower in the future, looking at this style of equipment can be beneficial.
Preparing New Carbon Media for Use
Once new carbon has been installed, it is essential to properly condition it:
Soak the carbon: Fill the vessel with water to submerge the carbon and allow it to soak for at least eight hours. This will remove many of the air pockets within the carbon, and total de-aeration may take over a week.
Backwash the carbon: Initiate a backwashing cycle to remove fines and stratify the carbon bed. The backwash flow rate should be sufficient for a minimum of 30% bed expansion, and flow rate should be done gradually until the desired flow rate has been achieved. The backwashing cycle should be continued until the water runs clear for at least 20 minutes, but we recommend 30-60 minutes. Conduct a turbidity test or use a white cup to inspect the carbon fines to ensure water clarity thorough the backwashing cycle.
Sanitization Of New Carbon
There are typically 2 options to sanitization of carbon media, steaming and hot water sanitization.
Steaming: Steaming is a highly effective method for GAC (Granular Activated Carbon) sanitization, reaching temperatures that kill most microorganisms, including thermophilic bacteria and penetrates areas where hot water would not contact. This process typically involves:
Temperature and duration: Carbon needs to be heated completely to 85°C (180°F), with steam cycles running for 8-10 hours at temperatures above 105°C (220°F). The maximum steam temperature should not exceed 110°C (230°F).
Procedure: The vessel should be backwashed before and after steaming to remove debris and fines. Ensure face piping and valves are sanitized by exercising them to expose all wetted surfaces.
Advantages: Steaming penetrates areas that hot water may not reach, especially useful for thorough sanitization in larger, complex systems.
Important steps: Include a complete cycle of backwash, settle, heat-up, steaming, cool down, and refill. Condensate should be removed during the cycle, and upflow steaming is preferred for more effective results.
Hot Water Sanitization: Hot water sanitization, while different, also provides effective GAC treatment and biofilm control. Here’s how it works:
Temperature and recirculation: Hot water should be at minimum 85°C (180°F); recirculating through the vessel until the exit temperature reaches 82°C or higher. When exit temperature is 82ׄ°C or higher, continue this process for 1-3 hours for new media, or longer (4+ hours) for older, compacted media.
Process: During recirculation, the vessel is filled, ensuring maximum contact with the GAC surface and internal components. Sample ports should be opened briefly during recirculation to expose all parts to heat.
Cooling phase: Hot water is pushed to the drain, gradually cooling for 45 minutes to an hour. Afterward, the vessel should be backwashed and rinsed to clear any remaining carbon fines or dislodged biofilm.
Controlling Microbiology in GAC Systems
GAC filters are effective at reducing chlorine in the upper portion of the bed and removing organic compounds, but this can create an environment conducive to microbiological growth if not managed. Proactive, routine sanitation practices are critical:
Routine sanitation: Sanitize regularly to prevent excessive biofilm buildup. Effective sanitization must address all system components, including face piping, valves, and interior surfaces to keep excessive growth of these organisms under control.
Monitoring and treatment: Total bacterial count in treated water can indicate biofilm shedding, necessitating immediate sanitation. Biofilms are almost unavoidable, so you must stay ahead of them.
Best practice: Ensure that the face piping has full CIP capability including chemical CIP without requiring chemicals for that CIP to come in contact with the GAC in the vessel.
Sterilization of GAC with Caustic
Caustic sterilization is another approach for deep cleaning.
Isolate the adsorber but leave it filled with enough water to completely submerse the GAC.
Add NaOH in a safe manner as detailed by instructions on the container or as prescribed by established procedures.
When the pH of the water has reached 12 or 13, stop adding caustic and allow the filter to remain in this state, off-line overnight.
Backwash slowly until effluent reaches an acceptable pH and put filter back on-line.
Addressing pH Changes with New Carbon
When new GAC is installed, it’s not uncommon to see a pH rise at startup. This can vary based on source water and carbon surface chemistry. To manage this:
Drain, fill, and soak cycles: Run these cycles to expedite stabilization.
Acid adjustment: In severe cases, lower inlet pH to speed up stabilization.
Product selection: If past installations experienced prolonged pH excursions, select GAC processed for faster stabilization.
Ensuring thorough and effective sanitation practices not only keeps water systems compliant but also enhances long-term performance and reliability. Whether through steaming or hot water, proper sanitization is a critical aspect of maintaining optimal GAC function and water quality.
Complete Water Solutions Can Help with Your Carbon Tower
Depending on where your water comes from, various pollutants can end up in your system. Carbon tower systems from Complete Water Solutions can remove some of the significant offenders from your water source. Our team at Complete Water Solutions can help you when selecting the right industrial water treatment. It is highly recommended that you consult professionals to find the best solution for your business. We offer many resources for choosing and determining the right system and solution. Get in touch with us today to get more information on your next steps.